Specifying The Right Aluminium Grade And Plastic Type For Medical Devices
14th Jun 2021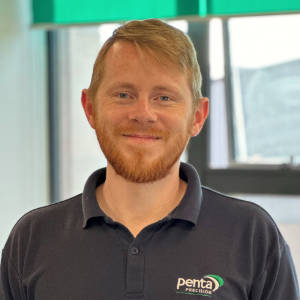
Is The Aluminium Grade I Want Available In The Form I Need?
You love the brushed aluminium finish on your top-of-the-range designer laptop. And you want the same finish for the high-end medical device you’re specifying.
But this may not be as easy as you think. The aluminium grade you want may not be readily available. Or the finishing may require special techniques.
Perhaps you’ve specified a particular grade of aluminium – such as 5251. And that’s all well and good if you want a medium-strength magnesium manganese alloy with high corrosion resistance, good ductility and formability.
But here’s the problem: 5251 is available only in sheets (and then only in thicknesses up to 5 mm). So it’s not the grade for you if your application involves machining big chunky blocks of aluminium.
Is There A Better Grade Of Aluminium For My Application?
Maybe you’ve specified 6061 because it’s a grade you recognise from aerospace, shipbuilding or construction. Problem is…6061 isn’t readily available in the UK because it’s a US grade (albeit one that is gaining popularity in Europe).
And are you really sure you want 6061? For certain applications, we would recommend 6082 instead because it’s stronger, more resistant to corrosion and 30% cheaper.
There are great benefits to be gained by speaking with experienced machining specialists before deciding on a particular grade of aluminium. A quick phone call can save you a lot of time and money.
Aside from answering your immediate questions, that handy phone call could alert you to possible prototyping, pre-production and production issues further down the line.
Am I Specifying The Right Type Of Plastic For My Project?
Specifying plastics can be just as tricky as choosing the right grade of aluminium…if not more so.
That’s because plastics are generally more challenging to machine than aluminium. They can move and flex during the cutting as primary manufacturing stresses are affected. So it takes skill and patience to machine plastics (and that’s assuming you’ve specified the right one in the first place).
Acrylonitrile butadiene styrene (ABS) is a case in point. You’ll find it in products everywhere because it’s a great all-rounder for lots of reasons: rigidity, impact resistance, insulating properties, abrasion and strain resistance, dimensional stability and surface brightness/aspect. What’s not to like?
So ABS has become a go-to plastic for moulders everywhere (though ASA offers better UV stability). And there’s the issue…moulding.
ABS is a moulding grade plastic. It’s for moulding, not machining (or at least not until it’s been moulded into something first). Specify ABS and you will most likely be offered a big bag of pellets. It has very limited availability in sheet, block or rod form for machining.
And that’s not the only problem with plastics. It’s just as easy to come unstuck when specifying different plastics by the sheet or rod as well…
Ask Yourself: Have I Allowed For Wear And Tear?
Let’s imagine you need machined plastic parts that are 12 mm thick. So you specify a plastic that is available in 12 mm sheets. So far so good. But when your machining supplier ships the finished parts, you’re underwhelmed. The finish is poor – too many scratches and even the odd gouge.
Not good. So what went wrong?
Here’s the reason: those plastic sheets will have had a hard life before they ever went anywhere near a machining shop. They’ll have been forklifted around a succession of warehouses, trucks and distribution centres. They’ll have been handled roughly…and the scars will show.
Furthermore, neither sheet nor round bar can be extruded exactly right (there is always variation). So the manufacturing tolerances are set to +/+: they are always slightly larger than the stated thickness or diameter:
- a 12 mm sheet would be +0.3 mm to +1.3 mm thicker
- a 50 mm raw rod would be + 0.3 mm to + 1.3 mm larger in diameter.
And this can lure inexperienced suppliers into a false sense of security. They think the extra thickness will give them enough leeway to tidy up the surface. Sadly, it won’t (and it’s certainly not enough to make a 12 mm sheet properly flat).
But experienced CNC machining specialists specify a thicker grade of plastic sheet than they need – a couple of millimetres extra on each side – so they can machine out all the nasty scratches and imperfections.
And they’ll handle the plastic with kid gloves. That means:
- using soft padding when securing the plastic for machining – instead of exposing it to raw, hard metal edges when clamping
- storing the plastic parts in protective bags to shield them from the day-to-day knocks that can happen in any factory.
Unhappy With Your Existing Suppliers? Download This Free Guide
Do your current machining suppliers scrutinise your RFQs meticulously and alert you to potential issues? Do they help you to solve those issues before they arise?
Or do they lack technical expertise and hard-won experience? Do they get slopy-shouldered and defensive when there’s a problem? Do they play the old ‘I just did what I was told’ card?
If you’re not 100% happy with your current suppliers, then it could be time to get a second opinion, time to bring in expert help.
Download your free guide to changing suppliers. It covers:
- what to look for in your new CNC machining suppliers
- why traditional methods of sourcing suppliers don’t always work
- key questions you should ask machining companies
- why you shouldn’t just rely on certifications (demand rigorous in-house inspection procedures and validated processes)
- good practice in procurement – how you can help your suppliers to help you.
Why Getting Penta Involved Can Save You Time And Money
Penta Precision is ISO 9001:2015 accredited for quality assurance. Our experienced engineers can alert you to potential design and engineering issues before they become costly, time-consuming and stressful.
Penta is different because we have tried and trusted validated processes:
• We communicate well
• We take care at each stage
• Our service is consistent.
Get expert help from Penta Precision