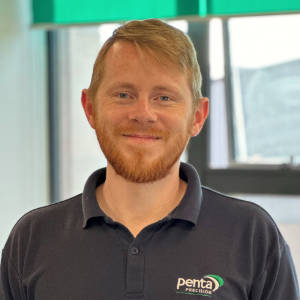
Getting The Fine Balance Right
It can be a tricky balancing act to specify components in industries where:
- there is a need for volume but also for safety
- competition is high
- the market is commoditised.
Designers and product development teams facing these challenges understand that precision machining tolerances must be detailed. And the datum must be precise. If they get any of this wrong, they risk compromising the product’s fit, form and function.
But these engineers also work on the basis that tolerances should also be as broad as possible where components are less important.
And we respect that: there are decades of combined wisdom and knowledge in major OEMs’ technical centres. They are rigorous in their approach because of the safety and cost implications.
But every tight tolerance adds cost to the equation. The tighter the tolerance, the higher the cost. So the temptation is for OEMs to specify easier tolerances where (in theory) they are less likely to matter.
Quite often they do matter though. And that’s when the OEMs’ procurement professionals call on us for help...
Unhappy With Your Existing Machining Providers? Download This Free Guide To Changing Suppliers
What Can Go Wrong With Engineering Tolerances
CNC machining tolerance issues typically involve 3D models that are not the correct size and/or geometry. Or the difficulties are down to technical drawings that lack crucial elements:
• missing specifications
• missing views (such as projected first or third angle views)
• no datum
• missing and incorrect dimensions or tolerances
• missing geometric tolerances
• no specific surface finish requirements (or any surface finish requirements at all, for that matter)
• missing or vague specifications for deburring and sharp edges.
Other Issues Involving Specifications
Material grades may not be specified. Or if they are, the material is specified in the wrong format (making it unavailable).
Or finishing specifications may be incomplete with regard to colours and thicknesses. The specifiers may not have considered fully whether a component is customer-facing or not. There may be anomalies or a lack of compatibility between the material grade and the finish specification.
And what if parts need to be bought in? The basic brief may be short on information with regard to the full specifications and preferred source(s) of those parts.
Crucial Stages: When Issues Are Likely To Arise
It’s the assembly stage that can often prove to be a watershed moment for OEMs and their existing suppliers. There may be:
- missing details of how interrelated parts interact
- issues with each component’s datum or tolerances
- mismatches in the geometric tolerances.
Field trials are another crucial stage. Ultimately, they are the real test of whether a component is going to work properly. Parts that seemed to pass muster at the assembly stage may be found wanting in real-world testing. So again, the OEMs and their suppliers seek our help.
Download Your Free Guide To Changing CNC Machining Suppliers
Download our free guide to finding the right CNC machining company for specialist requirements (such as medical devices). The guide covers:
- what to look for in your new CNC machining suppliers
- why traditional methods of sourcing suppliers may not be sufficient
- key questions you should ask your machining company
- why you should demand rigorous in-house inspections (and not just rely on certifications)
- good practice in procurement (looking further ahead).
Get Penta Involved
Penta Precision is ISO 9001:2015 accredited for quality and consistency. Our processes are validated:
- We communicate well
- We take care at each stage
- Our service is consistent.
Overcome your machining challenges – get Penta involved.