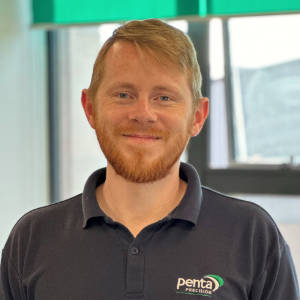
What Went Wrong? How Do I Fix It? Can You Help Me?
You’re having difficulties with a precision component for a critical medical device. The part won’t fit the assembly. Or the finish isn’t right. Or the quality/consistency is hit and miss. Or any number of other issues.
But your existing supplier – who perhaps has been reliable up until now – is pushing back: they did “exactly as instructed”, they protest. They followed your drawings/CAD models “to the letter”.
So what went wrong? And how can it be fixed quickly and cost-effectively? You want a second opinion – is the issue with the supplier, the drawings or both?
Misplaced Dependency On 3D CAD Software
Expert use of CAD is essential to ensure consistency of quality – especially in sectors such as medical devices.
There is no doubt that – in the right hands – modern CAD systems and 3D modelling have accelerated product development and made product design more accessible. Furthermore, 3D models can also help with regard to programming and setting operations. This reduces the time and cost needed to get a batch of components machined.
But CAD is not a magic wand: the detail has to be right…otherwise CAD can hinder.
A design that looks great as a 3D model may have hidden flaws. And those errors may become evident only later on when your precision machining supplier starts pre-production work on components for your new medical product.
And if that supplier simply ‘does as they’re told’ and machines the parts according to your drawing/model – without alerting you to any anomalies – then it will not end well. You will waste money and delay shipping.
Just because your designer didn’t account for the real-world variables that can impact on a supposedly ‘perfect’ CAD file.
How Detailed Are The Tolerances In Your Specifications?
The Devil is most definitely in the detail when it comes to how a model is finally drafted and the tolerances in CAD drawings/models. If you can’t see any issues then you may not be looking hard enough.
Tolerances of +/-0.1 mm may look ‘okay’ on a CAD file but they can come back to bite you when it’s time for the cutter to hit the metal (or plastic). At headline level, you may be perfectly happy with tolerances of +/-0.1 mm. But when it comes to the details, things can go horribly wrong…
What if a shaft is +0.1 mm and its intended hole is -0.1 mm? On paper, they both meet the overall tolerance – but in the real world, the shaft will be too large for the hole by 0.2 mm.
Now imagine a second scenario. In this case, the shaft fits the hole. So far so good in theory. But what kind of fit had you intended?
- forced fit (high interference) – a large temperature differential is needed, permanently joining gears or shafts (disassembly risks damage or destruction)
- driving fit (medium interference) – parts can be assembled with hot pressing (or substantial force if cold) for permanent mounting of gears, shafts and bushes
- press fit (light interference) – parts can be assembled with cold pressing (hubs, bearings, bushes, retainers)
- fixed fit – negligible clearance; parts can be assembled/disassembled with light pressing (plugs, driven bushes, armatures)
- similar fit – negligible clearance; parts can be assembled/disassembled with a rubber mallet (hubs, gears, pulleys, bushes, bearings)
- location fit – very close clearances for precise accuracy; parts can be assembled/disassembled without force – they will turn and slide when lubricated (precise guiding of shafts)
- sliding fit – minimal clearances for high accuracy; parts can be assembled easily and will turn and slide freely (shafts, sliding gears)
-
close running fit – small clearances, moderate accuracy; for moderate running speeds (guiding of shafts, spindles, sliding rods)
-
free running fit – large clearance where accuracy is not essential and there are high running speeds and/or large variations in temperature
-
loose running fit – larger clearances (pivots, latches, parts susceptible to corrosion, heat or contamination).
Asking Questions, Questioning The Answers
Good CNC machining companies – the kind you need to manufacture high quality components for medical equipment – make a point of asking the right questions. And they don’t just take the answers at face value.
With their heritage in precision machining, the care they take to get the job right (with good communication), they’ll want to play ‘Devil’s advocate’. They’ll ask questions until they’re happy that:
- they’ve shared their experience to second guess and assist in getting the job right
- potential issues have been ironed out
- quality and consistency can be assured
- the components can be machined as you intended.
That’s why buyers and specifiers of components for medical devices seek out Penta’s specialist expertise. It’s usually because something has gone wrong with a previous supplier at the prototyping or pre-production stage. The supplier didn’t ask enough questions. Or the right ones.
(And sometimes it’s the supplier who approaches us…because they’re having difficulties and need our help.)
Download Your Free Guide To Changing CNC Machining Suppliers
Finding the right CNC machining company for specialist requirements – such as medical devices – can be difficult and time consuming.
Download your free guide to changing suppliers. It covers:
- what to look for in your new CNC machining suppliers
- traditional methods of sourcing suppliers – and why they don’t always work
- key questions you should ask machining companies
- why you should demand rigorous in-house inspections (and not just rely on certifications)
- good practice in procurement (looking further ahead).
Get Penta Involved
Penta Precision is ISO 9001:2015 accredited for quality assurance. Our experienced engineers can alert you to potential design and engineering issues before they become costly, time-consuming and stressful.
Penta is different because we have proven validated processes:
• We communicate well
• We take care at each stage
• Our service is consistent.
Need more information? Contact Penta Precision