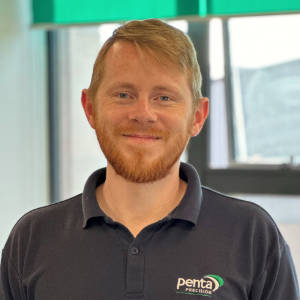
Are you designing parts that are destined for space travel? Satellites and other space components experience a unique set of conditions that necessitate careful design and manufacture.
Fortunately, here at Penta, we have loads of experience in supporting customers within the space industry to design and manufacture their machined components.
In this blog, I will look at the challenges and give my top tips on how to design a CubeSat including material selection and coatings.
The challenge
Components of a satellite and indeed all components for space are exposed to cosmic and solar radiation and extreme temperatures. They must be lightweight, yet durable, and of course, it’s not possible to nip up into space and do a quick repair. They must not fail.
The satellite itself, be it a conventional, large satellite or a nanosatellite (aka CubeSat), will house a payload of high-end electronics, a power system, and a communication link back to Earth.
As a designer working in the space industry, you’ve got your work cut out!
CubeSats
Many of our customers have opted for a CubeSat as it’s highly modular, from 1U (single unit CubeSats) right up to 6U (six units joined together) and has a much lower launch cost – they are designed so that they can ‘piggyback’ securely into a larger launch vehicle, via a dispenser.
How to design a CubeSat
If you’re designing a CubeSat or some other component that will be rocketing into space, there are some very important manufacturing decisions that you should consider.
One of the most important points is that it must conform to the standards of the dispenser, ensuring that it will fit securely and can be cleanly released into space at the right time. Therefore, when it comes to design and manufacture, tight tolerances are imperative.
It’s worth consulting with your CNC machining partner to discuss what tolerances are achievable with your chosen material and surface finish. You also want to ensure you fully trust your machining supplier as achieving tight tolerances is a skill that unfortunately not all companies display.
You can read more about tolerancing in our blog ‘Why tolerance matters’.
Space application design features
Of course, there will be variations in design between different space components and applications.
However, there are some commonalities and areas that are always worth considering.
Weight reduction
This is a very important aspect to consider in your design – how can you optimise it to reduce weight without compromising on functionality?
Consider hollowing out non-critical features of the component while maintaining structural integrity. This can be achieved with pockets, ribs, or internal channels.
Additionally, you can analyse stress concentrations and optimise wall thickness throughout the component. You don’t need to make all walls uniformly thick – use thicker sections where needed for strength and thinner sections elsewhere to save weight.
Strength
Of course the material selection and coatings will play a crucial role in strength (more on that later) but you can also optimise your design to maximise strength.
For example, design features such as sharp corners can create stress points that are more prone to failure under extreme conditions. Therefore, I recommend incorporating features such as fillets and chamfers.
Ribs and gussets can also be incorporated to enhance stiffness and reduce vibration susceptibility.
Paying close attention to the orientation of the part during launch and operation is also important. Can the design be optimised to minimise stress on critical features?
Thermal management
Satellites experience drastic temperature swings in launch and operation. Consider incorporating features such as internal channels or strategically placed fins to aid in heat dissipation or heat retention as needed. Also consider design features that accommodate thermal expansion and contraction.
What material is best for components going into space?
Another critical consideration is choosing a suitably space-resistant material that is also lightweight.
It’s a big ask for a material to be radiation-proof, vacuum-proof, able to operate in extreme temperatures (both very cold and very hot), as well as offering exceptional robustness, and weighing as little as possible.
But all of this is crucial for a CubeSat frame and other machined components for space.
Mostly, components for space are manufactured out of aluminium 7075, 6082T6, various grades of titanium (often Ti-6Al-4V or Grade 5), or ceramics. All these materials offer a good balance between strength and weight.
So, which one should you choose?
It’s important to be aware that there can be issues with ceramics giving off toxic dust when machined, so finding a machining company for ceramic components may be more challenging. It is possible to machine ceramics safely, but it requires specialist processes and equipment.
At Penta, we work with multiple grades of aluminium and titanium for space applications. See our materials pages to find out about some (but not all!) of the different materials we work with. You can also compare different grades of aluminium in our blog ‘Selecting an Aluminium alloy’.
A note about aluminium 6061
If you’re looking online for space-resistant materials, you’re bound to come across references to aluminium 6061 being used for components for space applications.
Aluminium 6061 is an American-wrought grade of aluminium that has similar properties to aluminium 6082. In the UK, 6061 can be hard to source and expensive. We recommend using aluminium 6082 as a more cost-effective and readily available alternative in the UK, with no compromise on performance.
Coatings for space components
It’s not just the material that helps to make a component suitable for space. In many instances, a component for space can be made better, or more suitable, by adding some kind of protective coating.
Coating or plating a component makes it possible to improve conductivity, manage temperature fluctuations, or resist corrosion. Often a space component will have multiple finishing processes applied to it to make it fit for purpose.
For example, many space components are hard clear anodised. Clear anodising gives a champagne colour to aluminium, providing a protective, corrosion-proof outer to the components.
However, it’s worth noting that anodising is a dip process – the components are dipped into an acid electrolyte solution – which means that specific areas of the component can’t be easily masked or left un-anodised.
Therefore, to allow for any necessary electrical conductivity and to ensure that a FIP gasket (form-in-place gasket) can be applied, components are machined again post-anodising.
A final layer may then be applied, such as an iridite coating. This is a very thin, invisible film that provides further corrosion protection without impacting the seal of a FIP gasket.
For more information about different finishing processes, take a look here.
Next steps
If you are designing a CubeSat or any space applications or components, you need to work with a trusted machining partner who has extensive experience in this highly demanding industry. This involves not only having the required skills to manufacture your part, but can also being able to help with creating a design suitable for machining.
Here at Penta, we offer both – a top-rated CNC machining service where we take care and offer consistent quality plus a Design for Manufacture service to help you get the most effective product in the most efficient way.
Our small, friendly team of estimators are on hand to have a no obligation chat about your project – give us a call on 023 9266 8334 or email .