Why tolerance matters: the why and how of specifying tolerances for CNC machining
21st Aug 2023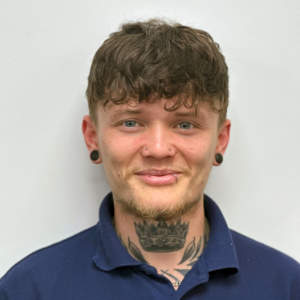
Tolerances – love them or hate them, they’re an essential part of CNC machining. In this blog I’ll cover what a tolerance is and why you need it, what a default tolerance is, what impacts tolerances and more.
What is a tolerance?
Let’s go back to basics for a minute…what exactly is a tolerance? To put it simply, a tolerance is the level of accuracy required for a machined part. Tolerances are needed because it’s impossible to manufacture any part with 100% accuracy (although CNC machining is the most precise manufacturing method).
Specifying a tolerance provides a margin of error which decreases the risk of parts not fitting or being fit for purpose. Tolerances usually dictate the minimum or maximum allowable dimensional limit which is expressed using ± i.e. ±0.08.
Tighter tolerances are usually specified when there are mating parts, where the component is safety-critical, or is part of a complex assembly. Specifying the correct tolerance will improve the fit and function of your part.
For context, a tight tolerance is typically ± 0.005”, although ±0.001” can be achieved.
What is a default tolerance?
A CNC machining supplier will usually have a default tolerance. For example, Penta Precision’s default tolerances are DIN-ISO-2768-mk. DIN-ISO-268 is an international standard created by ISO to simplify drawing specifications for CNC machining.
The m here signifies medium for linear and angular dimensions (e.g. internal and external sizes, diameters, radii, step sizes). To put this into context, for a linear dimension, this would be a tolerance of ±0.1 for a 0.5 to 3mm length and for a 1000 to 2000mm length, the tolerance would be ±1.2.
The k relates to features without individual tolerance indications, with k being the middle class. This includes straightness and flatness, perpendicularity and symmetry. For straightness and flatness on a length up to 10mm, this would mean a tolerance of 0.05 and a length of 300 to 1000mm, a tolerance of 0.6.
A default tolerance would usually be applied when a customer tells us they don’t require any specific tolerances for their components.
Why not always specify a tight tolerance?
Achieving a very tight tolerance is time-intensive, for the machinist and quality inspector, and therefore more expensive. Tight tolerances also invariably invite the need for more specialist equipment, particularly for inspecting. This will unavoidably increase costs. Where tight tolerances are necessary, this will be a cost that needs to be factored in. But for components that don’t need to fit keenly with other components, a more open tolerance would be appropriate, reducing machining time, and therefore costs.
For example, if you are machining a shaft that will be inserted into a tube, there will be a certain tolerance that will allow for the two components to function properly together when assembled. If the size difference between the two components is small, a tighter tolerance will be required. If close fitting isn’t required, a smaller shaft could be machined, and a wider tolerance applied.
What impact does material have on tolerances?
Your chosen material will have a large bearing on the tolerances available to you. For example, some engineering plastics are quite tricky to machine. They are more often affected by heat and moisture which can cause them to change dimension or lose shape as the cutting tool comes into contact. This can make it extremely challenging to hold tolerances.
Materials like stainless steel, on the other hand, are more stable during machining but may still require specific tooling and strategies. If you're working with this material, it's worth reviewing the requirements for stainless steel CNC machining early in the design process to avoid issues downstream.
Different materials have different standard tolerances. If in doubt, it’s best to work with an experienced CNC machining company who can guide you in both material selection and tolerance specification. For example, when working with aluminium, using a specialist aluminium CNC machining service can help ensure tolerances are achievable while maintaining cost efficiency and structural integrity.
What impact can surface finishing have on tolerances?
Finishing processes such as anodising can add thickness to a component. Therefore, this needs to be considered when specifying machining tolerances. Finishing processes usually come with their own tolerances which can be used to help you specify the machining tolerance.
Tolerances: coming unstuck
When buyers or design engineers approach Penta because they are having quality issues elsewhere, it can often be tolerances that are causing problems.
When tolerances aren’t dealt with correctly on the part of the designer or the CNC machining company, things can go wrong very quickly.
The two main issues we encounter are:
- The CNC machined component supplier is not keeping tolerances which is causing major issues at assembly stage, ultimately leading to delays and spiralling costs.
- The customer has not specified tolerances or has incorrectly specified tolerances. The machinist makes the parts to drawing but they’re not fit for purpose and the customer feels let down by their supplier.
Feeling intolerant about tolerances?
Choosing the right precision machining partner to help you overcome tolerancing challenges is imperative. Here at Penta Precision, we eagerly follow our 3Cs which allows us to deliver a superior level of service and quality at all levels, including tolerances:
- Communication – we review and understanding your required tolerances before we undertake the project. Where tight tolerances are specified, we’ll always discuss with you to ensure they’re proportionate and help you manage costs.
- Care – we discuss geometric tolerances at an interdepartmental level when quoting a project to ensure we know what can or can’t be met. Care is taken at every stage, from quoting through to production and inspection.
- Consistency – our processes are robust and followed to the letter including our rigorous quality inspection procedures. See Penta’s Proven Process to see how we work.
If you need a helping hand with specifying tolerances for your project, speak to one of our experienced engineers for a free consultation – call 023 9266 8334.