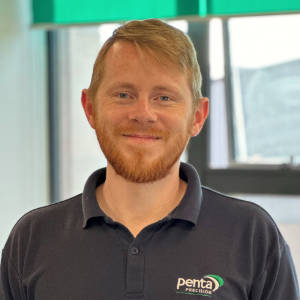
Cost-effective precision machining: a guide to reducing your quote
Let’s face it, no one wants to be paying more for the same thing. So it can be disappointing when the price of your machined components goes up or a quote takes you by surprise.
The truth is, whilst the headlines have calmed down, we’re not yet out of the woods with the rising price of raw materials and energy. Both of which have a part to play in the cost you pay for your CNC machined parts.
When quoting a part, there are three main factors that make up the cost:
- Raw material – the price of which can fluctuate and unfortunately when this goes up, it must be passed on
- Machining time – how much time will it take up on a machine, how much time will a skilled machinist need to spend on this part?
- Finishing processes – to be factored in as an additional process
Frankly, there’s little you or I can do about the cost of materials. Of course, as a CNC machining company, we do shop around within our list of vetted suppliers.
Where you may have some control as a designer is by reviewing the design of your precision machined component. Often there are ways to adapt your design to reduce costs without affecting the form, fit or function of your component.
In this blog, I’ll take you through my top tips for reducing the price of your machined components by reviewing the design.
Design your components in relation to standard plate, bar and tube sizes
An easy start is to consider the standard sizes of plates, bars and tubes. If it is possible for your component to align with standard sizes, you may be able to both reduce machining time and material wastage, and consequently reduce the cost per component.
Turned component example
For example, if your aluminium turned component has an outside diameter of 33mm, this would be machined from a Ø38mm stock bar.
However, if the design allows, you could reduce the outside diameter of the finished component to Ø31.75mm (Ø1.25″). This is a standard size for aluminium bar, meaning that you would reduce the amount of raw material required, and therefore the cost, and potentially also cut machining time.
Milled component example
Similarly, if you are designing an enclosure that requires milling and your design stipulates a depth of 48mm, a standard 50mm billet would usually not be suitable: we generally allow 3-5mm of material to hold the part for machining.
Therefore, the next available size billet would be 57mm, meaning a lot of additional raw material is required (higher cost and more wastage).
In this case, I would ask if it were possible to change the design to a 45mm depth, which would enable the machined parts supplier to use a standard 50.8mm billet, and still have enough material to hold the part.
Leave some faces ‘as stock’ where possible
Another way to optimise your raw material usage is to leave all or some faces of a component ‘as stock’ i.e. not machined.
This is a particularly good option for components that are part of an assembly where some or all faces will never be seen.
Let’s return to that 33mm diameter turned component. Sizing down to a diameter of 31.75mm and leaving as stock would save costs in two ways: a smaller diameter bar of raw material could be purchased, and less machining time would be required.
In the case of a milled component, there may be a customer-facing ‘front’ that needs to look aesthetically pleasing, but the back may rarely or never be seen, and could therefore be left unmachined.
As well as reducing machining time, this approach also decreases tool wear – reducing cycle times and associated consumables. This can reduce the overall cost per component.
It’s worth noting that some materials are more suitable for this than others. Aluminium, for example, usually has a cleaner finish than stainless steel, so there may be more opportunities where an aluminium component can be left as stock than stainless steel.
Tolerance
One final aspect to consider is the material tolerance. If your component has a blanket tolerance of ±0.1mm, but the tolerance of the stock material is ±0.2mm, you will need to decide whether it is appropriate to relax the tolerance of your design, either for the whole component or on specific faces.
If not and the tolerance must be met across all faces, leaving as stock would not be an option.
Simplify your design
Once you’ve checked that your raw material usage has been optimised as much as possible, there may be other features of your design that could be changed to help get costs down.
An example of how a design could be simplified is if it features complex pockets or recesses to reduce component weight. It may be possible to adjust this to a simple circle or square which would be far simpler to machine.
While the precise ratio between weight and strength could be compromised, it may well be possible to create a design with comparable strength, that is just a little weightier than ideal.
Of course, it may not always be acceptable to make this compromise, but where budget is tight and there is some design flexibility, small savings such as this can be very handy.
Other design considerations
Other aspects of the design to review are material selection, tolerances, surface finish and corner radii. My blog post Electronic Enclosure Design for Machining has some excellent suggestions for ways you could adjust the design of an electronic enclosure to keep costs down, and many of these tips are applicable for other types of component too.
Purchasing approach
Modifying your design isn’t the only way of cutting costs. Greater economies of scale can be achieved from ordering in a different way.
Many of our customers choose to place call-off or scheduled orders; they anticipate demand and place an order annually and then either contact us incrementally for a portion of their order or pre-arrange delivery dates throughout the year.
By doing this, you get the best of both worlds because you benefit from bulk order pricing but you can still spread the cost over the year.
Partnering with a CNC machined parts supplier
When the economic environment is challenging, every detail counts. At Penta Precision, we’re not just a machining parts supplier, we’re your partners in cost-effective design. Our experienced team is ready to collaborate with you, offering insights, expertise, and innovative solutions.
Don’t let high costs hold back your vision. Reach out to our Estimation team on 02392 668 334.