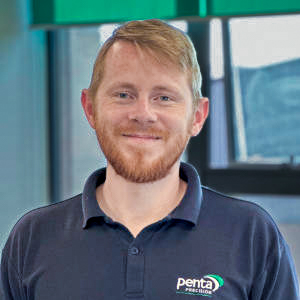
Design choices made early in a project often have the biggest impact on cost and performance. Even small details like a chamfered edge can improve how a part functions, fits, and holds up over time. If you’re sourcing or designing custom machined parts, understanding chamfers is a simple way to improve both quality and efficiency.
In this guide, you’ll learn what a chamfer is, how it differs from other edge types, and why it matters in CNC manufacturing. We’ll explore how chamfers affect performance, safety, cost, and overall part quality. You’ll also get practical insight into designing chamfers for better results across different materials and production volumes.
Need to source custom machined parts? Get in touch with the team for a custom quote.
What is a Chamfer?
A chamfer is an angled edge that connects two adjoining surfaces, usually cut at around 45 degrees. It's used to remove sharp corners, making parts safer to handle and easier to assemble. In simple terms, the chamfer meaning in manufacturing is all about improving usability and function with a clean, sloped transition.
Chamfered vs. Other Edges
Chamfers are commonly compared to fillets and bevels, but they serve different purposes. A chamfer edge is straight and angled, a fillet is curved and smooth, and a bevel spans a longer distance between parallel surfaces. Knowing when to use each type is key to getting the best fit, performance, and finish.
Chamfers are ideal for guiding parts into place and reducing the risk of edge damage. Fillets are better for reducing internal stress in parts under load. Bevels are often chosen for aesthetic reasons or where larger angled joints are required.
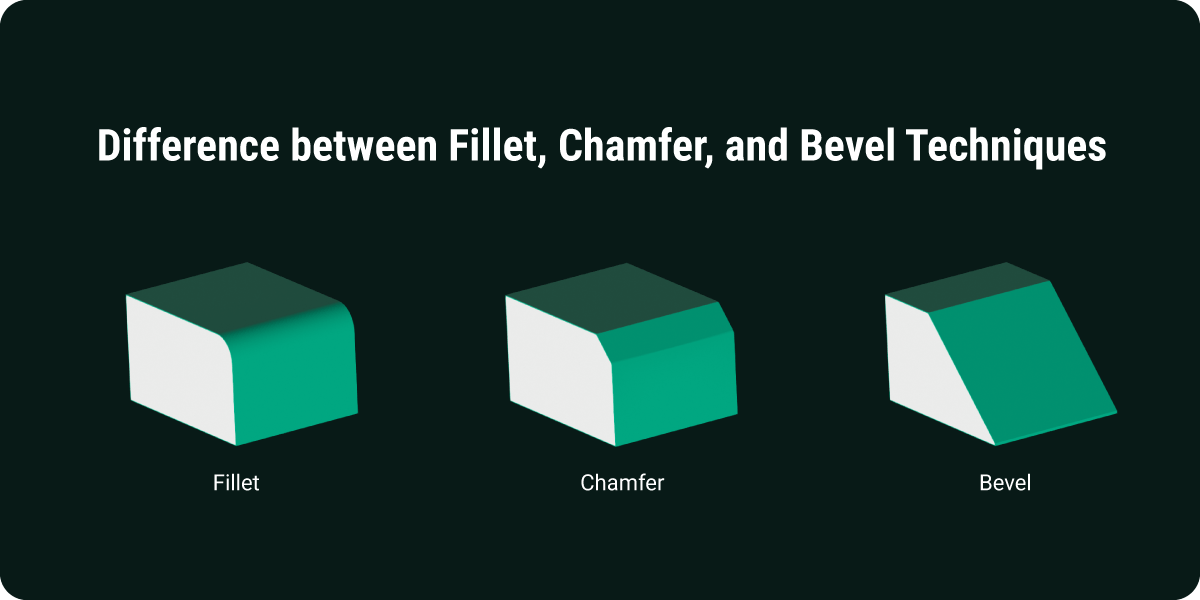
Angles and Dimensions
Chamfers are most often cut at a 45-degree angle, but they can be adjusted to suit specific part designs. A typical callout might say "1.0mm x 45°," though you can specify length and angle independently depending on your requirements. Keeping chamfer dimensions standard across parts can reduce programming and machining time.
Larger chamfers are useful for parts that need smoother guidance into assemblies. Smaller ones are perfect for simply removing sharp edges without affecting the part's profile. Choose a chamfer size that balances function with ease of production.
Tolerances and Specs
Chamfer tolerances are generally more forgiving unless the edge plays a critical role in part alignment or assembly. Specifying tighter tolerances can increase machining time and inspection requirements, which adds unnecessary cost. For non-critical edges, general notes like “Break all edges” often do the job just fine.
When precision is important, be clear about the required depth, angle, and chamfer length. Use measurement tools like chamfer gauges or optical comparators to check dimensions accurately. But where high accuracy isn’t essential, simpler tolerances save time and money.
Functional Uses
Chamfers do much more than remove sharp edges, they improve how parts fit, feel, and perform. Whether you’re working with mechanical assemblies or aesthetic parts, chamfers are a smart design move. In this section, we’ll look at the main functional reasons to include a chamfered edge in your parts.
Assembly Fit
A chamfered edge acts like a lead-in, guiding components into place during assembly. This is especially useful for press fits, dowels, and shaft-and-hole alignments where accuracy matters. It reduces the risk of misalignment or damage, helping parts fit together smoothly.
You'll commonly see chamfers used on bolt holes for faster alignment. They're also added to tube inserts or housings for easier mating. Pin or shaft leads in mechanical assemblies are another frequent use case.
Stress Relief
Sharp internal corners often concentrate stress and can lead to cracking under load. A chamfered corner helps soften that transition and spreads stress more evenly across the surface. This reduces the risk of failure, especially in brittle or lightweight materials.
hamfers work well in parts exposed to moderate mechanical loads. While fillets still offer better performance under heavy, dynamic stress, chamfers are often sufficient for static or low-stress parts. They add durability with minimal effort or added cost.
Safety Benefits
Sharp, unfinished corners can easily cause cuts, snags, or discomfort during handling. A chamfered edge removes this risk and makes the part safer to work with at every stage, from production to installation. This is especially helpful in materials like aluminium and stainless steel, where machined edges can be razor sharp.
You'll often find chamfers on fastener heads to make them easier to grip. They're also used on the edges of housings and covers to prevent injury. Handheld tools and fixtures often rely on chamfers to improve user comfort and safety.
Visual Appeal
Chamfers create sharp, intentional-looking transitions that give parts a clean, high-quality finish. They help surfaces meet in a balanced, symmetric way and can enhance the overall appearance of machined products. Many industries use chamfered edges to signal professional craftsmanship and attention to detail.
They're especially effective when used to create sleek transitions between angled surfaces. Designers also use chamfers to improve the look of exposed corners or part outlines. In branded or polished products, consistent chamfers support a more premium finish.
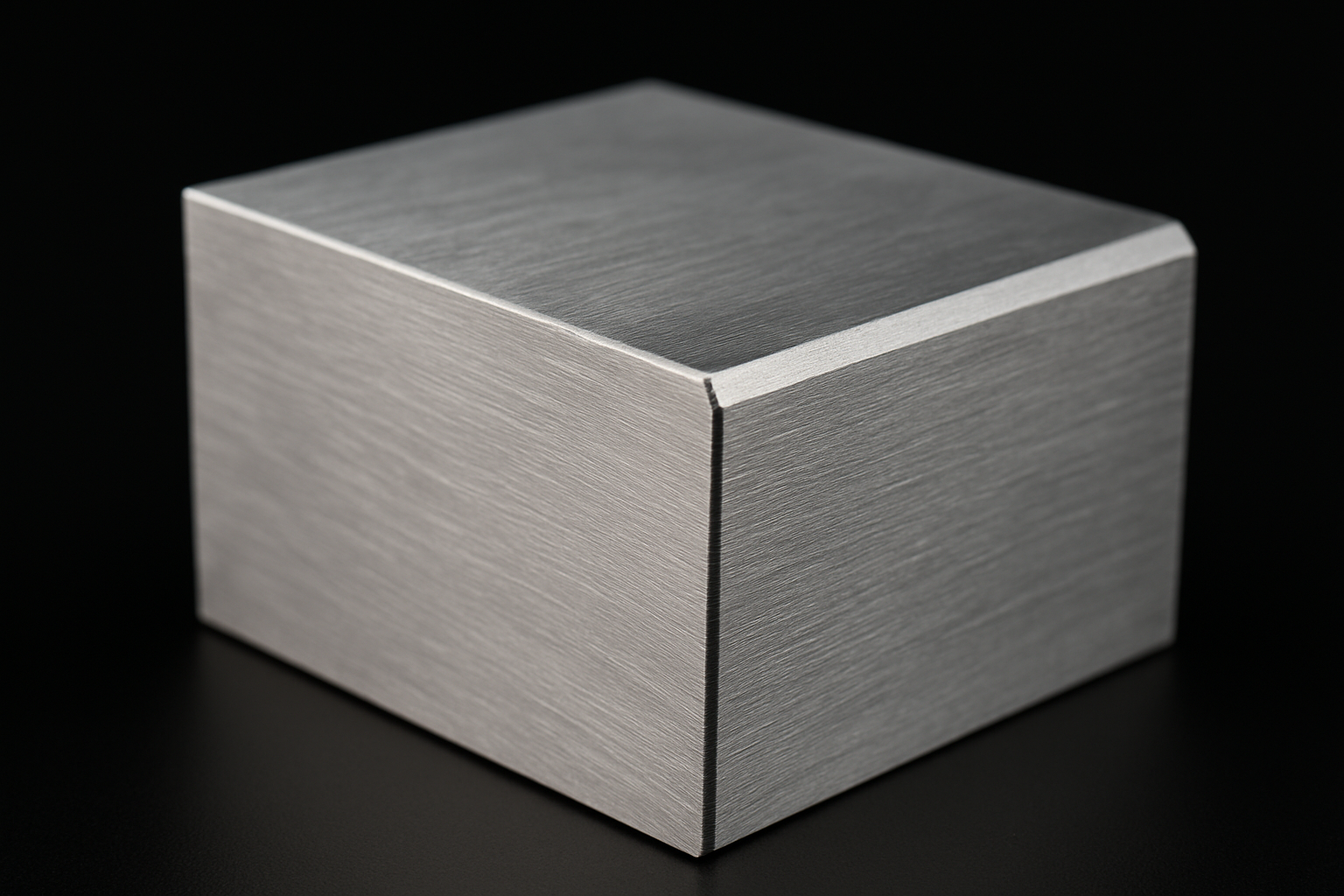
Materials and Tools
The material you're working with will directly affect how easily a chamfer can be applied. Some materials machine cleanly, while others require more care and specialised tooling. Choosing the right combination of material and chamfering tool ensures a better finish and longer tool life.
Hard Materials
Hard materials like stainless steel and titanium need more robust tools and slower feed rates to achieve clean chamfers. These metals are prone to work hardening, tool wear, and thermal stress if not machined carefully. In stainless steel machining for precision parts, using coated tools and optimised speeds is essential for maintaining accuracy.
Typical challenges include:
- Work hardening during cuts
- Shorter tool life
- Surface microcracks if speeds are too high
Soft Materials
Materials like aluminium and engineering plastics are easier to chamfer and allow for faster cutting speeds. These softer materials often require less aggressive tooling, making the process more efficient. That's why chamfering is widely used in aluminium machining for CNC components.
Watch for issues like:
- Smearing or gumming in plastics
- Overcutting on soft edges
- Slight deformation at very small chamfer sizes
Chamfer Tools
Most CNC setups use dedicated tools to create chamfers efficiently in a single pass. These tools include chamfer mills, spot drills, and countersinks, each suited to different angles and part types. Choosing the right tool reduces setup time, tool changes, and the risk of inconsistent edges.
Common chamfering tools include:
- Chamfer mills
- Spot drills
- Countersinks
Corners and Internals
External chamfers protect edges from chipping, reduce handling risks, and make parts easier to package. Internal chamfers help components like screws, pins, or connectors align more smoothly during assembly. Both types improve part function and usability without requiring complex design changes.
Useful internal examples:
- Screw starts for blind holes
- Lead-ins on locating pins
- Smooth entry for press-fit components
Cost Considerations
Chamfers are generally low-cost to machine, but the way you design and specify them can influence their overall cost. Simple specs are easier and quicker to produce, while overly complex or tight requirements can drive up machining time and tool wear. In this section, we'll look at what really affects the bottom line when it comes to chamfers.
Volume Impact
When used correctly, chamfers can actually reduce part costs in high-volume production. They streamline assembly, improve fit, and reduce the need for post-processing or touch-ups. This makes them especially efficient when you're using CNC milling services for larger batches.
High-volume advantages include:
- Lower labour per part
- Fewer rejected assemblies
- Easier part packaging and shipping
Design Complexity
Simple chamfers with uniform angles are much faster and cheaper to machine. But if your part includes multi-angled, deep, or inconsistent chamfers, you'll likely face increased programming and machining time. Keeping chamfers consistent in size and angle helps improve inspection speed and process reliability.
Try to avoid issues like calling cosmetic chamfers critical when they don't need to be. Varying angles or depths across different part features also adds unnecessary complexity. A uniform approach to chamfer design will always save time and reduce risk.
Tolerance Costs
Tight chamfer tolerances can slow production and increase tool wear. They may also require additional inspection, which raises overall cost without always improving part performance. Unless the tolerance directly affects function, consider using a general break-edge callout instead.
Some good tolerance practices include:
- Use standard sizes like 0.5mm or 1mm x 45°
- Label critical chamfers separately from cosmetic ones
- Apply looser tolerances on non-functional features
Material vs. Tooling
Material selection plays a big role in chamfering cost, especially when it comes to tool wear and cycle time. To keep costs in check, choose the correct tool coating for wear resistance, avoid specifying tiny chamfers in very hard materials, and combine chamfer passes with other operations where possible. These small adjustments can help maintain edge quality while keeping production efficient and budget-friendly.
Designing Chamfers for Performance and Efficiency
Designing effective chamfers starts with understanding their purpose. Whether you're breaking edges for safety, guiding parts into position, or improving a component's visual quality, knowing the goal helps shape the right approach. Once that's clear, you can choose the simplest and most cost-effective chamfer that meets your requirements.
Smart chamfer design includes using standard angles like 45° to reduce tool changes, avoiding overly tight tolerances unless necessary, and including chamfers early in the CAD model. These small decisions improve machinability, reduce production time, and help avoid last-minute design changes. By planning chamfers from the start, you save time, reduce waste, and produce more reliable parts across every batch.