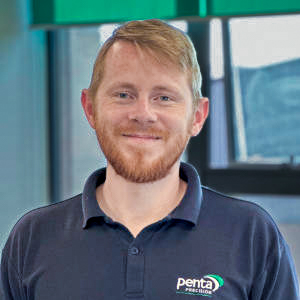
Edge treatments often get overlooked, but they can make or break the performance of a machined part. Choosing between a chamfer and a bevel affects everything from assembly ease to safety and long-term durability. A clear understanding of the difference helps you avoid costly mistakes and improve results across your manufacturing processes.
Chamfers and bevels differ in geometry, function, and how they’re machined. Each serves a specific purpose depending on the material, application, and performance requirements. Whether you’re working on aerospace components, medical devices or industrial parts, knowing when to use a chamfer vs bevel edge can streamline production and improve part quality.
Want to get a price on our services? Get in touch with the team for a customised quote for your part.
Key Takeaway: The Difference between Bevel and Chamfer
Chamfers are short, angled cuts that improve safety, handling, and part alignment. Bevels are longer slopes that allow for stronger joints and better fitment, especially in welded assemblies. Choosing the right edge reduces cost, simplifies machining, and improves part performance.
What is a Chamfer?
A chamfer is a small, angled cut applied between two perpendicular surfaces, usually at a 45-degree angle. It removes sharp corners to make parts safer to handle and easier to assemble. Chamfers are widely used in CNC milling due to their simplicity, consistency, and efficiency.
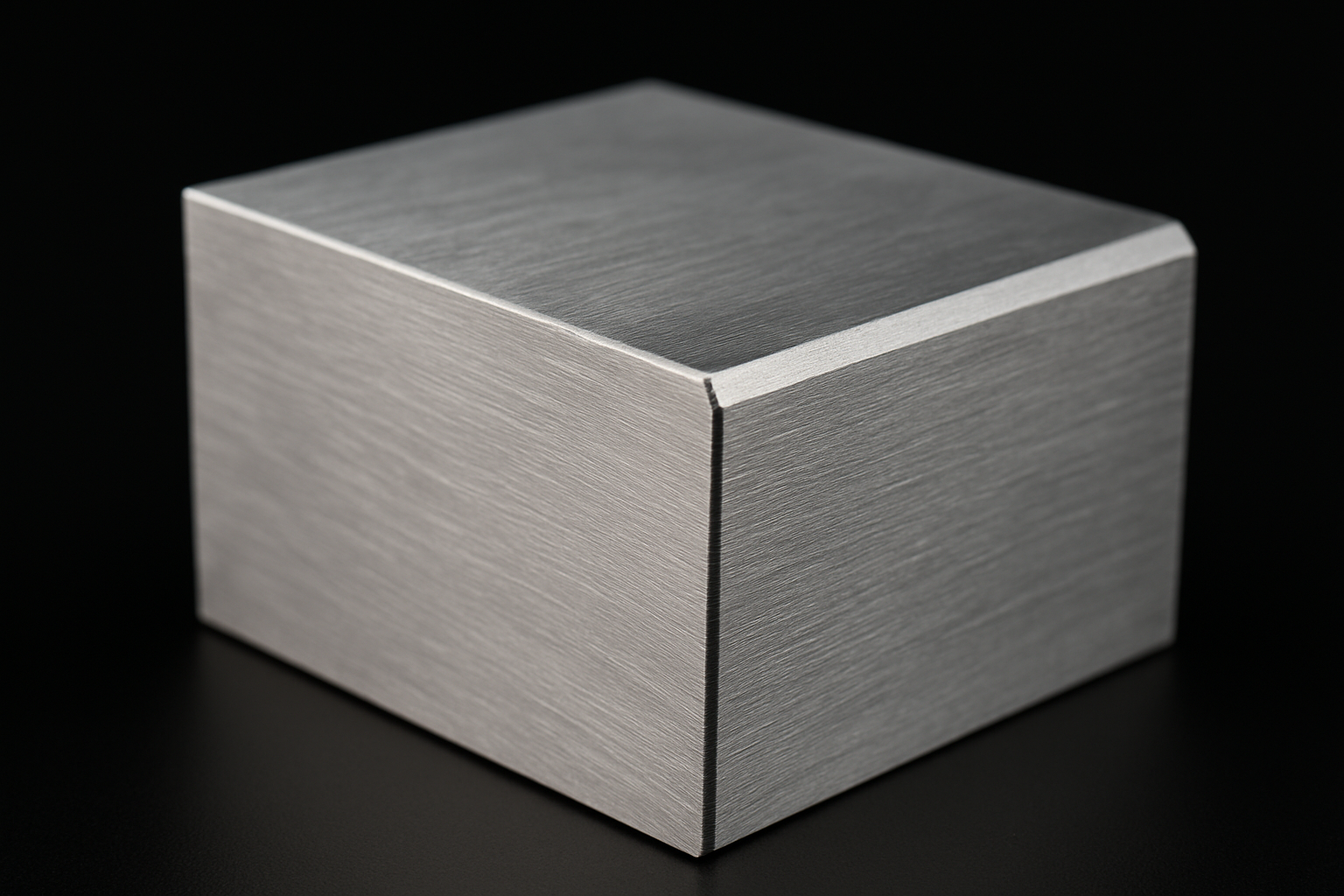
Key Characteristics and Advantages of Chamfers
Chamfers reduce the risk of injury by softening sharp edges on metal or plastic parts. They also help relieve stress concentrations, improving part durability under load or during assembly. In addition, chamfered edges give machined components a neater, more finished appearance. Factoring in the design and material considerations of chamfers in machining can help optimise results across large production runs.
Key benefits of chamfers:
- Safer handling and reduced injury risk
- Better part alignment and easier fastener insertion
- Lower machining time with standard tooling
When to Use a Chamfer
You should use a chamfer when a part needs to guide easily into another component during assembly. They’re also effective when working with brittle materials, helping to prevent cracking and corner chipping. Chamfers are a smart option for parts requiring high efficiency, repeatability, and clean, professional results.
Examples of Chamfer Applications
Chamfers are often applied to bolt heads to avoid cracking and make tool engagement smoother. Brake pads use chamfered edges to minimise noise, vibration, and uneven wear during operation. You'll also find chamfer bevel features on aerospace and electronic housings for both functional and visual purposes.
What is a Bevel?
A bevel is an angled cut that connects two parallel surfaces, forming a longer and more gradual slope. The angle can vary depending on the part’s design, but 45 degrees is commonly used. Bevels are often chosen when strong joints, precision fitting, or welding are required.
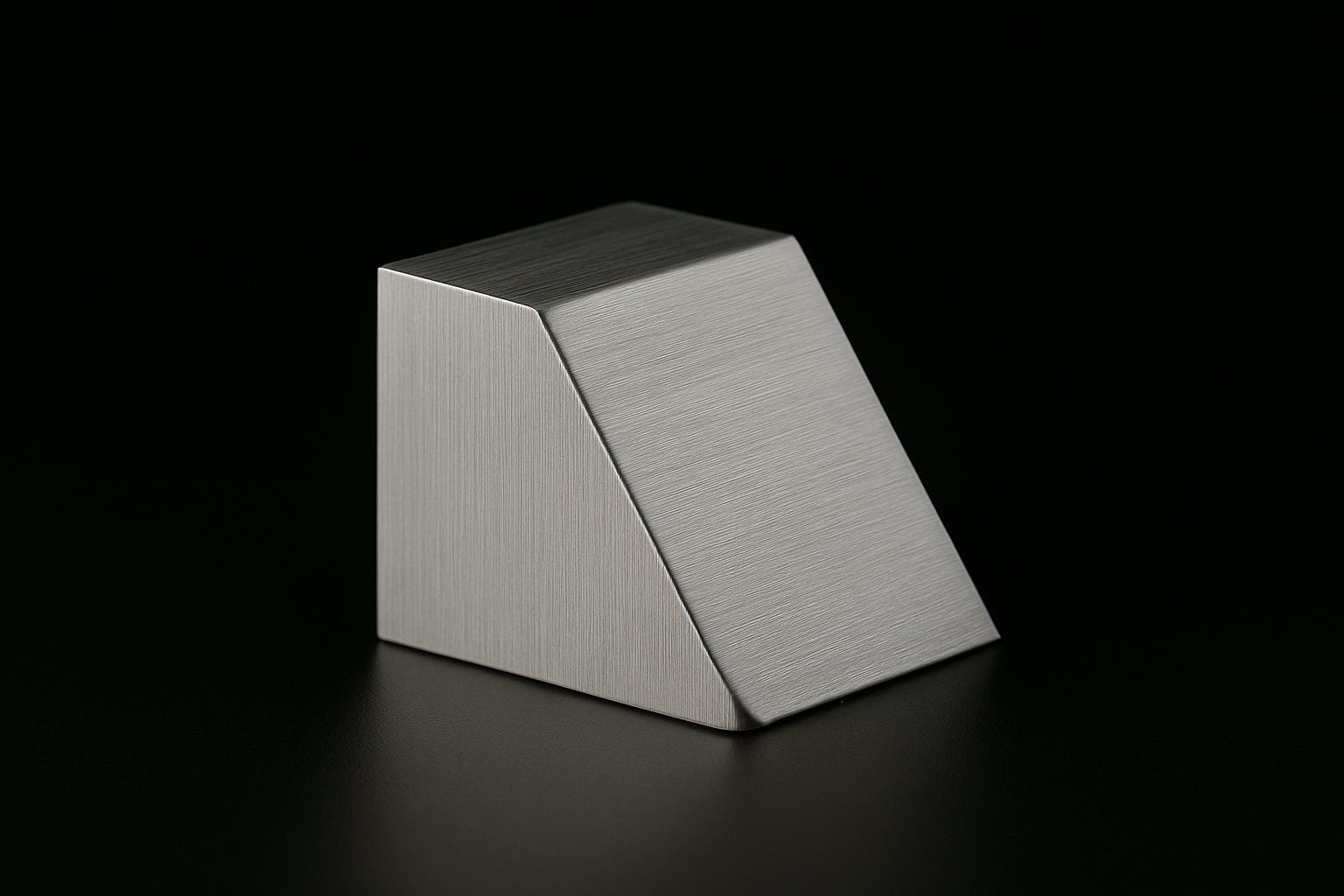
Key Characteristics and Advantages of Bevels
Bevels create extended transitions that improve the structural integrity and fit of assembled parts. They are especially useful in applications where weld strength or joint depth is important. Bevelled edges also help reduce friction and wear in parts that move or engage frequently, and are often integrated into CNC machining services for complex parts.
Advantages of bevels include:
- Stronger joints and better weld prep
- Tapered edges for smooth engagement in assemblies
- Reduced friction in gear and bearing systems
When to Use a Bevel
Choose a bevel when components need to align precisely or form part of a welded assembly. They are ideal for panels, structural frames, or pipework where strength and accuracy are key. Bevels are a strong choice when working with tough materials, especially in stainless steel machining for precision parts.
Examples of Bevel Applications
Bevels are often applied to pipe ends to allow for welding or tight pressure fits. Bevel gears use angled tooth profiles to maintain smooth motion while reducing noise and wear. You'll also find bevel and chamfer edges in structural parts used in construction, mining, and heavy machinery for durability and clean alignment.
Chamfer vs Bevel Edge Differences
While chamfer and bevel are often confused, they differ in both geometry and function. A chamfer connects perpendicular surfaces and is generally short and shallow, while a bevel connects parallel surfaces and extends further across the edge. Chamfers are quicker to machine, whereas bevels typically require more material removal and precise tools.
Key differences to keep in mind:
- Chamfers = quick, clean cuts; Bevels = longer, structural slopes
- Chamfers = safer edges for handling; Bevels = stronger joints for welding
- Chamfers = less material removal; Bevels = more complex tooling
How to Choose the Right Edge for Your Part
The right edge depends on your part’s function, the material used, and your manufacturing goals. If the part will be handled frequently, assembled quickly, or used in a visible application, a chamfer is typically more effective. If structural strength or weldability is a top concern, go with a bevel.
Think about whether the part needs safe handling or structural alignment. Consider whether your priority is cosmetic appeal or functional performance. Time, tooling complexity, and overall cost are all important factors when deciding between a chamfer and bevel.
In addition to chamfers and bevels, fillets are often worth considering. Understanding the trade-offs between chamfers and fillets in machined parts can lead to better design decisions.
Optimise Your Design with the Right Edge
Including the right edge in your design phase can save time, money, and headaches. Chamfers are often added directly to CAD drawings and machined in a single pass, making them ideal for efficient production. Bevels may require multiple passes or specialised machines but offer structural advantages in return.
Standardising angles, designing in edges from the start, and working with a partner skilled in CNC milling for precision components all contribute to smoother production. These steps minimise errors and reduce lead times in the workshop. They also help maintain consistent quality and keep machining costs under control.
Working with Penta Precision gives you access to experienced engineers, 5-axis capabilities, and full machining support under one roof. Whether you need rapid prototyping or full-scale production, their ISO 9001:2015 accredited team helps you get the job done right. You benefit from a streamlined process and dependable, high-quality results.