Quality Control in CNC Machining: Inside Penta Precision's Proven Process
27th Jun 2025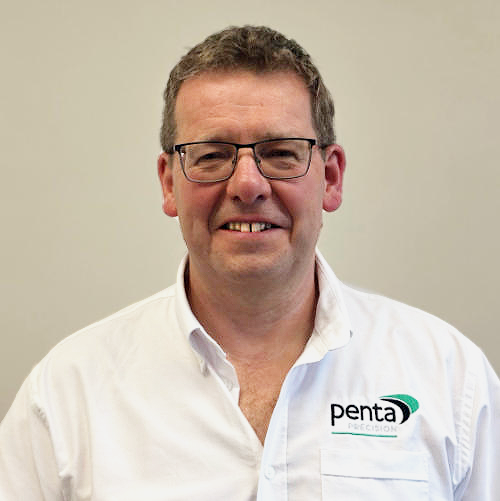
At Penta Precision, quality is more than a department. It’s the backbone of everything we do. From our very first discussions with customers through to final inspection and delivery, we’ve developed rigorous processes to ensure precision, reliability, and trust in every part we produce. In this blog, we share how quality is built into each stage of the Penta Proven Process, offering insights into why our customers place their confidence in us for critical projects.
If you have machining requirements and want to work with a partner committed to quality at every level, contact us today.
Quality Starts from the First Interaction
At Penta Precision, meeting customer expectations is woven into the fabric of how we operate. Quality is not confined to our inspection department—it’s present in every stage of our process. Quite simply, we want to get it consistently right for our customers. As Peter Drucker famously said, “the purpose of a business is to create and keep a customer.”
Manufacturing is a diverse sector, and every company has its own unique requirements. To meet these varied needs, our quality process starts right from the very first conversation.
Understanding Customer Fit and Requirements
When we begin discussions with potential customers, we carefully assess whether our services align with their requirements. For example, if a customer requires components the size of a tractor, another specialist like Sheffield Forgemasters may be more suitable. But when there’s a good fit, we invest time in understanding what makes each customer unique.
Managing Documentation and Standards
We pay close attention to documentation requirements. For many customers, the paperwork accompanying a product—certifications, inspection reports—is as crucial as the component itself. When preparing quotes, we check for any customer-specific standards or specifications that might be new to us. All drawings and specifications are securely archived for full traceability.
Reviewing Drawings and Creating Quotations
We rigorously review drawings for anomalies, missing details, or features needing clarification. Where required, concessions or production permits are noted in our quotations. Our Estimation and Account Managers, all experienced engineers, produce fully costed quotes that already contain about 80% of the detail needed for CNC manufacturing. For larger projects, we gather our heads of department to align our approach.
Engaging Quality Departments and Planning
We also proactively engage with our customers’ quality departments to clarify fit, form, and function requirements, along with any critical features. As we quote, we plan potential jobs into our live production schedule to maximise our chances of meeting deadlines. Quotations include detailed notes on part numbers, revisions, prices, concessions, and what’s included in our price. We always follow up to ensure our quotes meet the customer’s needs and to discuss moving forward. Often, as projects develop, revisions of the quote are required to be ready for an order to be placed.
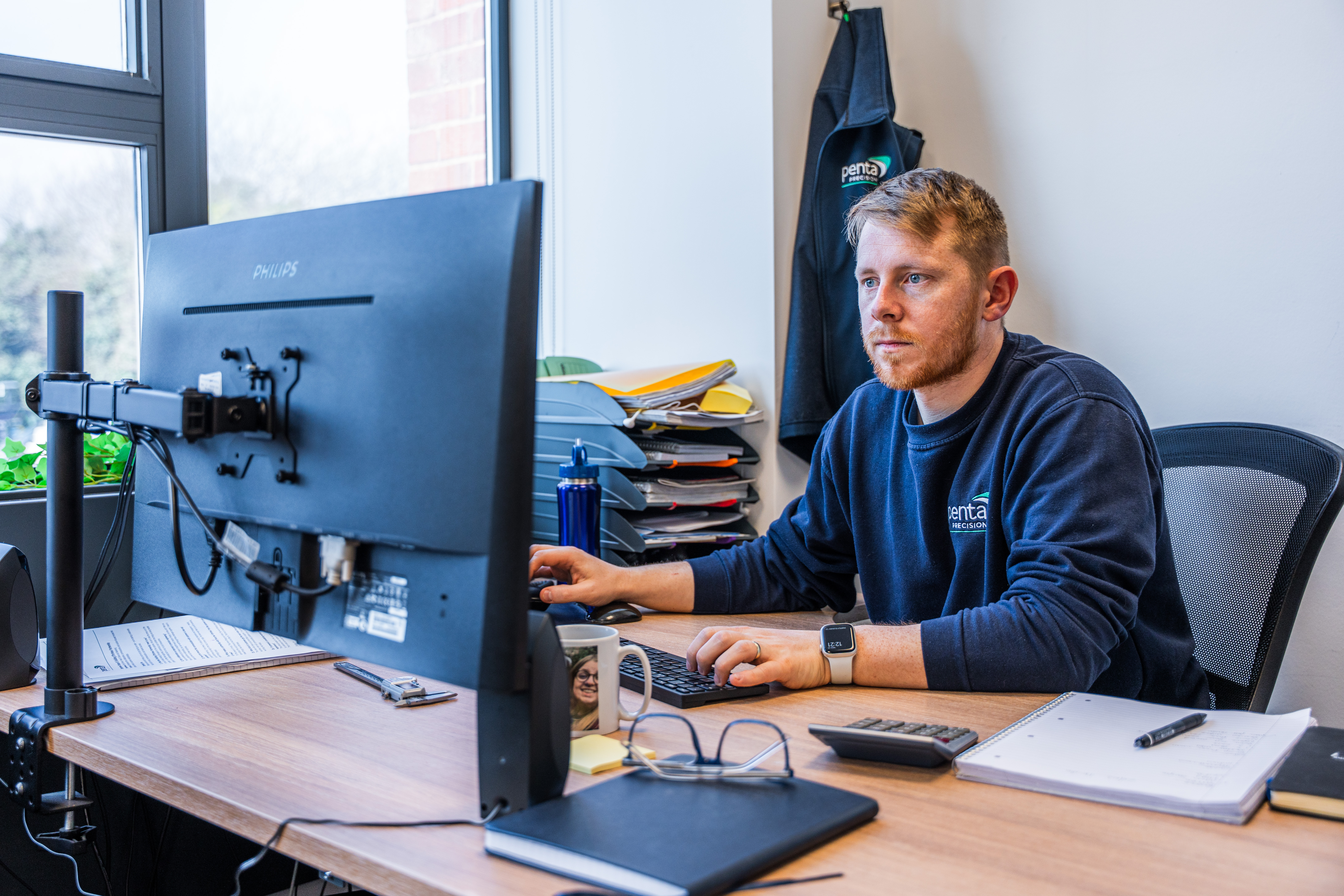
Quality During Order Processing
Once an order is placed, we carry out a thorough contract review. We cross-check the customer’s order, our quotation, drawings, specifications, and all account details to ensure everything is aligned—from documentation requirements to delivery and invoicing details.
The Estimation and Account Manager reviews the project and captures any additional details for communication throughout our process. The order is then programmed into our live production schedule, and a Sales Order Acknowledgement is issued.
Quality as Production Preparation Begins
When an order reaches production preparation, our team refines the initial 80% plan to 100% completion. Our preparation process includes a detailed checklist, sometimes spanning up to four A4 pages.
We order raw materials, fixturing materials, bought-in parts, and any project-specific tooling or gauges well in advance—typically 7 to 10 days before the scheduled start date. Sourcing materials has become more complex in recent years due to geopolitical changes. We have found that materials sourced from Europe, Japan, certain Asian tiger economies, and North America demonstrate consistently high quality in alloy content and heat treatment conditions. In contrast, materials from newer entrants like China and India can sometimes exhibit variability in alloying content, heat treatment, and resistance to corrosion or mechanical issues.
Specifications are checked, electronic drawings are prepared, and job-specific notes are added to works order routings. Setting and in-process inspection sheets are prepared to ensure a robust production and inspection plan. For significant contracts, we also hold all-hands coordinating meetings to align our approach.
In a high-mix, dynamic subcontract environment, building robust plans is essential to manage the variation and deliver consistent results. At the end of the preparation process, typically after 72 hours, if our lead time needs adjusting due to any material delays, we reschedule and inform our customers accordingly.
Quality During Production
Material Traceability and Preparation
All materials used at Penta are purchased with Certificates of Conformity and EN 10204 Type 3.1 Inspection Certificates for full traceability. Materials are booked in and assigned a unique Goods Release Number (GRN), marked accordingly, and tracked throughout the process.
Fourteen days before manufacture, project packs are issued to the shop floor. Raw materials, tooling, and gauges are gathered 12 to 48 hours before production to help machinists focus on the task at hand.
Skilled Personnel and Standardised Workstations
We employ CNC programmer setter operators across our factory to ensure we have the expertise required for the diverse nature of our work. Each machine workstation is standardised for work holding, equipment, and tooling, supporting consistent and controlled processes.
First-Off Inspections and Verification
Skilled personnel program, set up, machine the first-off components, and inspect them to verify compliance with the customer’s specifications. All inspection equipment is calibrated and externally verified. Once satisfied, the machinist seeks verification from dedicated “customer’s eyes” first-off inspectors following a standardised process. Given the variety of engineering specifications and customer requirements, this first-off inspection is critical in a subcontract environment.
The first-off process is followed at each stage of manufacture. After a first-off is approved, machinists closely monitor the first 3 to 5 components to ensure the robustness of the manufacturing plan. Details of setups, photographs, and notes are recorded to aid future repeat orders and maintain consistency.
Continuous Feedback and In-Process Checks
Throughout production, CNC setter operators are encouraged to annotate works orders and update setup sheets as part of our closed-loop feedback system for continuous improvement. If there are tooling breakages, tool changes, or process changes, a new first-off inspection is conducted for approval.
In-process inspections continue throughout the batch, with all personnel using calibrated equipment for checks. On the rare occasions when non-conformances are discovered, production halts, and a formal non-conformance process is initiated to resolve the issue. Parts are then passed to the next operation or, if subcontracted, undergo intermediate inspection before being sent out. Components are always washed and cleaned to meet contract requirements.
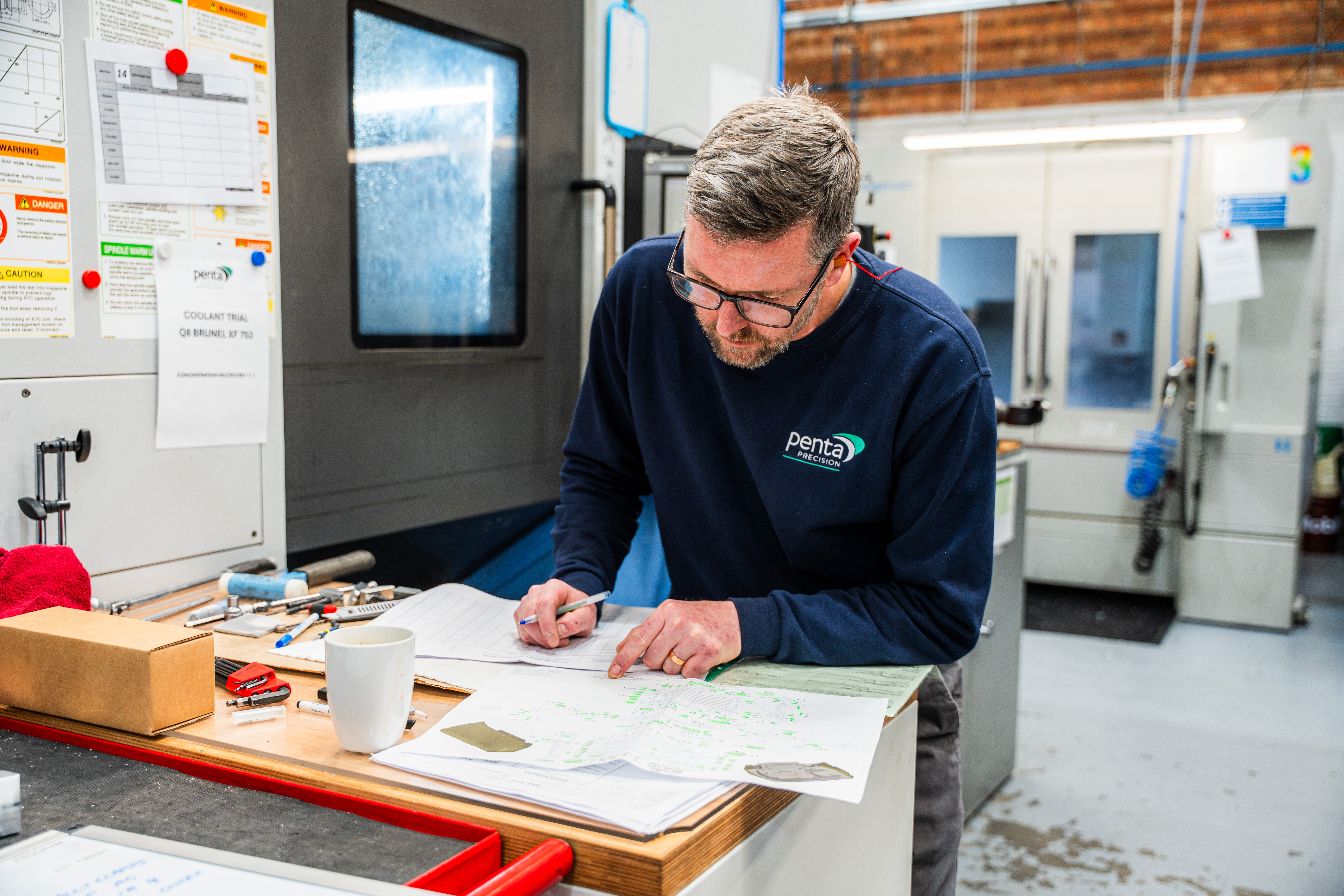
Quality in Subcontract Operations
For subcontract operations, our quality process begins as early as the quotation stage. We obtain supplier quotes and lead times and ensure that our partners work under strict confidentiality agreements. The RFQ process involves understanding several critical factors:
- Suppliers work with us under an NDA agreement
- We build working relationships with subcontractor personnel
- Anonymised drawings are shared
- Any processing allowances required through Penta internal manufacture
- Fixturing and in-process handling issues to be considered
- Spares required to ensure the batch quantity is returned
- Packing and carriage requirements are considered to keep products safe in transit
Before sending items out for subcontract processing, components are inspected to confirm they meet requirements. Purchase orders, together with detailed processing packs, accompany goods to subcontractors. Once returned, all subcontracted items undergo a full inbound inspection to ensure they meet specifications.
Quality at Final Inspection
Final inspection is conducted by our dedicated “customer’s eyes” inspectors using externally calibrated equipment. Inspections follow a standard batch sampling work instruction process or are tailored to specific customer requirements. If inspectors are not entirely satisfied, they reach out to customers for guidance and direction.
In the rare event that non-conformance is identified during final inspection, a full 100% inspection is implemented for the batch. The root cause is determined, and both immediate and permanent corrective actions are taken. We prepare all necessary customer documentation, including certificates of conformity, material mill certificates, and FAIR reports, in line with customer contracts.
All finished components are booked into stock, marked with a GRN number, and works orders are completed, passed on for feedback and archiving.
Quality in Storage, Packing, and Delivery
Products held in stock for scheduled, call-off, or Kanban deliveries are packed and stored with care. Customer-specific packaging, documentation, and carriage requirements are noted on customer accounts and integrated into manufacturing routings. Two dedicated goods-in/goods-out employees handle the picking and packing of outgoing orders to ensure components arrive safely and on time.
Quality Through Continuous Feedback
Throughout our manufacturing process, skilled machinists discuss updates and improvements with team leaders, noting changes on hard-copy works orders. This feedback loop is reviewed by production engineering and estimation teams to determine whether master part records should be updated.
If significant issues occur, such as multiple parts needing re-machining, additional billets being required, fixes exceeding three hours, trends being identified, or customer non-conformances being received, an internal non-conformance report is raised. Within 24 hours, an 8D investigation meeting is conducted to identify root causes and establish both short-term corrective actions and long-term solutions to prevent recurrence.
Quality Embedded in Our Culture
At Penta Precision, quality is built into our entire operating system. Our Core Values ensure we recruit and mentor the right people. All departments participate in weekly or fortnightly meetings to track progress against departmental scorecards, improvement projects, and self-development plans while discussing opportunities for improvement and solving issues.
Each quarter, the company and departments set priority projects that align with the business plan. Employees’ involvement in these regular meetings helps leadership determine the right priorities for the business.
We also hold quarterly State of the Company meetings to communicate progress and future plans. Employees are involved in developing, documenting, training, and following standardised working procedures throughout the business. Regular quarterly appraisals and personal development discussions help our team grow and sustain the high level of quality we promise.
This relentless focus on quality at every stage is why our customers trust Penta Precision with their critical projects—and why “Excellence Engineered” is more than a tagline; it’s the way we operate every day.