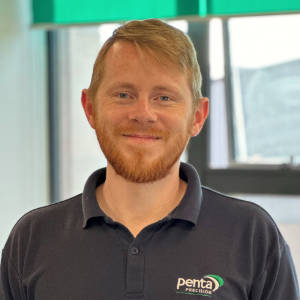
Whether you’re a professional buyer or a design engineer, you are probably feeling that there is a constant pressure to keep costs down while not compromising quality. When it comes to purchasing machined components, this can be a challenge as some of the main manufacturing cost factors – raw material and energy – have shot up in the last year.
In this blog, I’ll take you through the considerations in your project that will affect price and importantly, some points you can consider that could bring the price down without sacrificing quality, form, fit or function.
How complex the component is
The design of a component will determine how difficult, or not, it is to machine. That’s not to say that you must simplify your component. Of course I always recommend that you don’t over-complicate the design, but sometimes there are no options for simplifying without compromising the quality or functionality.
So what can you do in this case? The more pertinent question might be: which CNC machining supplier can work with a complex design and still find ways to keep the costs down?
Choosing a machining company that uses 5-axis technology is a good starting point. A 5-axis machine will be able to take on more complex geometries and machine them in one go, rather than the machinist having to manage multiple set ups on 3- or 4-axis machines. This will be a considerable time-saving factor, and saving time on a machine saves money.
Accessibility Controls
The player supports TAB to change the controls.
Update Required
To play the media you will need to either update your browser to a recent version or update your Flash plugin.
In this video you can see how using a pyramid fixture on a 5-axis machine is enabling the machining of three aluminium enclosures simultaneously, machined from a single set up.
Using 5-axis technology decreases risk because it makes it possible to machine components in a single operation. By contrast, multiple set ups increase the risk of error, meaning scrap rates may be higher and quality may be lower from companies that are less used to managing complex geometries.
Sometimes multiple set ups are required, whether that is due to machine availability or the component itself. But this needn’t spell disaster. A good machinist will create clever yet easily repeatable fixturing solutions which will lower error rates. A fixture holds a component in place so that it’s put in the machine in the right place time after time.
How much human intervention is required
Reducing human intervention is generally a significant cost saver. It has the dual benefits of increasing spindle running times and reducing the chance of errors.
Not all human intervention can be removed. The initial preparation, set up and first-off processes are always required, but from then on, allowing the machine to run is generally the answer to more repeatable processes, particularly when it’s a complex component. And again, robust processes are likely to save money – particularly for subsequent orders where problems have already been troubleshooted.
However, it’s worth noting that more complex parts will still require careful programming, set up and checking. The run time may also mean that machining hours are still high. In some cases, operator time may be minimal but a longer set up time by a skilled engineer may be required.
Which material you choose
Evidently some materials are more expensive than others. Sometimes only a more expensive material will do when the application requires a very specific set of properties.
However, in my experience, people often have chosen one material and are not aware that another cheaper material would also be suitable. For example, we are often approached by people wanting their high strength component to be machined from titanium. Titanium is high strength and lightweight (therefore has a superior strength to weight ratio) BUT it’s expensive. When we go into the detail with them, it often transpires that the component doesn’t need to be particularly lightweight. In this case, stainless steel is often a far more appropriate choice. It still has exceptional strength – in fact the highest strength stainless steel is stronger than titanium – but it doesn’t have the price tag of titanium.
Another example is copper which is known for its superior thermal conductivity. Sometimes only copper will do but, in many cases, an aluminium alloy may have sufficient thermal properties. Compared with copper, aluminium is comparatively low cost, more readily available and easier to machine which means shorter run times and tight tolerances are more easily achieved.
The grade of your chosen material is also an important factor. Most materials have many different grades – each with varying properties and different price points. Find a machining company who is happy to take the time to talk you through your options so you can achieve the right level of performance at a lower material cost.
How much inspection or certification is involved
Of course, inspection is critical and shouldn’t be skimped on. My blog post ‘How to ensure consistent quality from a CNC machining provider’ gives a good overview of inspection processes.
It’s worth taking the time to implement the right level of inspection for the application. Talk to your machining company about this and agree the number of parts per batch that need to be inspected. They will be able to guide you on this and help you achieve the best value for money without risking the quality of your component.
Certifications could include: material certificates, standard inspection, dimensional reports, FAIRs (first article inspection reports), and any custom reports you may require. Which of these certifications are needed are often industry and component-specific. But it’s worth bearing in mind that the more certification required, the higher the cost. Speak to the machining supplier to find the appropriate solution for you.
Purchasing approach
How you buy your machined components can also have a considerable effect on the price you pay. There are certain ways of purchasing that offer greater economies of scale. One approach that we have found to work very well for our customers is call off or scheduled orders. This works by placing a yearly order and then either contacting your supplier for components as and when you need them, or pre-arranging with your supplier to deliver batches of your order throughout the year. Buying this way means you benefit from the reduced price per part of a bulk order, but you spread the cost of the parts over the year rather than facing high upfront costs.
Others choose to bulk buy upfront and keep it in stock themselves which can have an even more significant reduction on the unit price, although obviously this is a significant upfront cost.
Many manufacturers are choosing to reshore their components for the stability of having a UK-based supplier who are less resistant to shocks overseas or shipping disruption. A UK-based supplier may have a higher cost per unit than a supplier in the far east (although maybe not as big a difference as you’d think), but the significant shipping times and growing uncertainty can often outweigh the benefits of buying overseas. My blog ‘What’s the point of reshoring your manufacturing?’ goes into more detail about the reasons it might be time to consider reshoring.
As you can see, there are many factors that will affect the cost of your CNC machined parts. Another that I haven’t covered in detail here, is optimising your design where appropriate. There are many small changes that can be made to a design that could bring down the price of a machined component such as consider where more open tolerances can be applied. Our handy guide ‘How to cut costs on your machined components’ covers these design considerations in more detail.
Want to chat all of this through with someone who knows their stuff?
We love chatting through projects, problem-solving and advising on how we can work together to achieve your goals. All of my team are time-served engineers, speak to one of us on 023 9266 8334