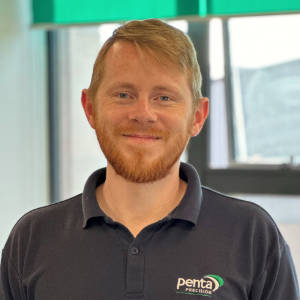
If you’re designing an electronic product, particularly one with a plastic housing, there’s a good chance you’re looking at ways to dissipate heat; and a heatsink may be at the top of your list. Heatsinks are designed to conduct heat away from a component, usually through the addition of fins or pins on one side of a component to increase the surface area and conduct heat away, providing an effective and cost-efficient solution.
But efficiency and value for money are only achieved when considerable thought has been applied to the design of a heatsink. In this blog, I’ll take you through the key considerations for custom heatsink design.
Material selection
Choosing the right material for your heatsink is crucial. Key considerations for material selection for any part include physical properties, raw material costs, availability, and machinability.
Of course, at the top of the list for physical properties for a heatsink is thermal conductivity. Copper is well-known for its superior thermal conductivity amongst other favourable attributes.
However, there are some significant drawbacks to copper: it can be challenging to machine compared to other metals, it’s not the most readily available and it’s also amongst the most expensive metals.
So, what’s the alternative? Unless you absolutely need the highest thermal conductivity of copper (i.e. when the environment of the application is itself warm), an aluminium alloy may be a deserving substitute with sufficient thermal conductivity, along with other benefits. Compared with copper, aluminium is comparatively low cost, it’s readily available and is easier to machine which means shorter run times and tight tolerances are more easily achieved.
Heatsink pin & fin design: managing deep channels
When designing your heatsink, it’s likely you’ll want lots of deep fins or pins to increase the surface area and create greater cooling efficiency. But this must be considered alongside the practicalities of machining. If your heatsink design includes channels that are particularly deep or narrow, the machinist will need to use custom tooling which can add considerable cost to an otherwise simple design. Additionally, the deeper the tool goes, the slower the tool feed rate which could significantly increase machining time and therefore, cost.
This means it may not be worth the additional cooling achieved for the cost it will incur. If sufficient cooling can be achieved with wider channels, less deep pins or fins, this will be a much more cost-effective strategy.
Surface finish
Another consideration of heatsink fin design is their width. Narrow fins have low rigidity, which may mean that they vibrate during machining. This can make it hard to hold tight tolerances and achieve a specific surface finish.
If the fins can’t be thicker, rethinking the surface finish can be a simple cost saver. Most drawings we receive have a standard drawing border stating a surface finish of Ra1.6µm, also known as a ‘good machined finish’. But is this necessary for your application?
The majority of heatsinks will have at least some sections that are not customer facing, or can be considered less important when it comes to surface finish. In these cases, you could relax the surface finish to Ra3.2µm or greater. This will also allow for the machining of narrower, taller fins.
Make sure you specify which surfaces of your heatsink are customer facing or need a higher spec finish within your drawing so the machinist can take greater care on those faces. And equally remove waste material faster on the less important faces, saving time on the machine and reducing unit cost.
Finishing
After the machining process is complete, many customers choose to have their heatsink plated. Plating avoids the component suffering from corrosion or tarnishing, and some types of plating can also increase the electrical conductivity of the part.
If the heatsink is part of an enclosure, plating or other finishing processes may also be chosen for aesthetic properties.
Plating does involve the addition of a thin layer of material, which can slightly increase the size of the component. For a component with tight tolerances or exacting dimensions, it’s important to find a supplier who is experienced in machining parts with plating allowances.
Next steps
If you’re designing a custom heatsink for manufacture, you need to partner with an experienced CNC machined parts supplier. Here at Penta, machining design advice is part of our standard service. We can help you design a heatsink that not only delivers the functionality required but also help get the project within budget.
Working with Penta will allow you to benefit from our superior service, encompassing communication, care and consistency.
Find out more about our custom heatsink machining service
If you’re looking for a machining company who can help ensure security in your supply chain and work with you to achieve the best form, fit and function for your component, call me and my team on 023 9266 8334 or email .