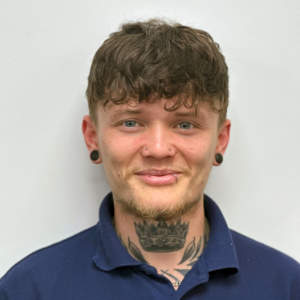
Have you ever marvelled at the sleek finish on your favourite gadgets? This level of finish is achieved from a process that is part science, part artistry. I’m talking about plating.
In this blog, I’m going to take you through what plating actually is, why you might choose plating as a finishing process for your next CNC machining project, the factors that affect the final plating finish, and how you can allow for plating at design stage.
What is plating?
Firstly, let’s make sure we’re on the same page. Plating is a common finish used for CNC machined components, a surface covering process where a thin layer of metal is added after machining.
There are several different forms of plating or coating including various types of anodising (notably Hard Anodising and Sulphuric Acid Anodising), chromate and non-chromate conversion, chrome plating, electroplating and electro-polish.
What are the benefits of plating?
Plating can enhance both the functionality and aesthetics of a CNC machined component.
One primary advantage is the decorative quality it imparts to surfaces, allowing for a diverse choice of finishes and textures.
Beyond aesthetics, plating can significantly improve corrosion resistance, protecting components from environmental factors and extending their lifespan.
Additionally, it can enhance durability, ensuring that a machined part can withstand a suitable amount of wear and tear for the application.
Why is plating a specialist process?
People often perceive plating to be similar in approach to precision machining. The reality is that it requires a very distinct set of skills. Plating requires a unique blend of craftsmanship and technical expertise to carefully manage multiple variables and control factors.
Colour match anodising – specific colours can be chosen for visual reasons or branding
The final plating finish is dependent on the following factors:
- The grade and source of the component’s raw material
- The geometric shape of the component
- How the component is held, supported, and fixed through the plating process
- Where the item is positioned within the processing vessel
- How the component is orientated throughout the process
- The other components that are processed within the same batch
- The skill and experience of the individual performing the process
- The industries and market sectors usually served by a processing company along with the type and nature of the work they regularly perform
- The unit price per item you are willing to pay for the process.
Brass, for instance, is often selected for its excellent machinability and compatibility with various plating finishes. Achieving the best results starts with high-quality brass machining, as surface finish and dimensional precision directly influence the outcome of subsequent plating processes.
The tighter the post-plating finish tolerance or the more aesthetically perfect the desired result, the more care, time, control, and therefore cost is involved. For example, the consistently beautiful, brushed aluminium finishes on Apple products are no accident, they have invested millions of dollars into developing the production process.
Building plating into your design: tips for designers
Hard anodise – strengthen the component and protect it
If your plated or coated components have finished sizes with less than 50 microns total tolerance range, or if you are producing a customer-facing component where aesthetics are important, here are some of the main considerations:
- Think about plating process requirements during the draft design stage. Engage with a competent plating company or a one-stop machining service provider to understand any potential processing issues and gain agreement on how to plan for consistent plating in the design
- State on the drawing if the finish sizes are pre or post-plating
- Larger parts being electro-plated may need two dedicated blind tapped holes at either end of the component to guarantee a good electrical connection and remove any opportunity for arcing and damage
- For plated components, only specify tight tolerances if necessary
- Discuss plating allowances (growth per face in the plating process), both with the plating company and the machinist. Include processing notes on the drawing
- As tolerances become tighter, there is a need to process components in their own individual batch and not mixed with other dissimilar parts
- Where tolerances are critical, post-plating grinding and honing may be required to guarantee consistent results.
- Unless necessary, don’t specify threads with class fits. There are multiple tolerances interacting when a screw and nut are assembled
- If the aesthetic finish is important, include notes on the drawing and:
- Carefully select a plating company to partner with who typically processes that type of work
- Discuss directly with the plating company how the part will be processed. Can it be jigged on hidden features? You may need to consider dedicated blind tapped fixture holds
Choose a one-stop shop to benefit from expert advice on design for manufacture and finishing processes
Surtec 650 or alacrom – primer treatment for further treatments to be applied
At Penta, we work with a network of carefully selected plating and coating suppliers. All parts are subject to our rigorous quality procedures and go through a full inspection before being dispatched, ensuring we deliver outstanding quality finished components time after time.
If you’d like a no obligation chat about your next CNC machining project, get in touch with our experienced engineers on 023 9266 8334 or email .