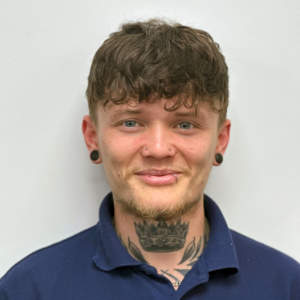
I speak to a lot of purchasing managers who have been disappointed by their current CNC machining supplier. The most common thread is overpromising and underdelivering on quality. Being promised the Rolls Royce of components and receiving a Vauxhall Nova.
Have you been in this situation?
If so, I completely understand how frustrating and stressful it can be. Exceptional quality isn’t just a ‘nice to have’. As a buyer, you’re relying on quality components for the reliability, consistency and performance of your product.
In this blog, I’ll share what good quality assurance looks like so you can make sure you choose a supplier who will deliver the quality you need.
Quality assurance and industry standards
This is probably the first thing you’ll want to be looking at when sizing up a potential CNC machining company to work with.
Reputable CNC machining suppliers proactively prioritise robust quality assurance (QA) measures for consistency of quality.
ISO9001 is the globally recognised standard for quality management. When a CNC machining company has this certification, they have demonstrated the required level of documented processes and traceability.
I’d be very wary of a machining company that doesn’t hold ISO9001 certification. For the record, Penta meets the requirements of ISO9001:2015.
Industry-specific certifications
Industry-specific certifications can offer an extra layer of assurance but don’t assume that a company without a certification specific to your industry is no good.
AS9100, a well-known aerospace industry certification, far surpasses ISO9001 and demonstrates an unwavering commitment to precision, reliability, and exacting standards. A buyer in any industry will benefit from this certification.
The key is not to be blinded by specific industry certifications (or lack of). Some companies may lack a particular industry certification but boast strong specialisations in other relevant sectors.
Process control
If I had to identify one aspect that will have the single greatest impact on the consistent quality of CNC machined components, it is robust and repeatable processes.
Having first-rate quality some of the time isn’t enough. So how is a prospective CNC machining partner ensuring consistency when it comes to quality?
When starting up discussions on working together, these are two of the key documented processes you’ll want to discuss:
- Documented processes for repeatable setups - meticulously documented setup procedures for complete repeatability and eliminating human error.
- File saving procedure - securely saved machining program and associated data ensures program retrievability and reproducibility, enabling repeatable setups and consistent quality across the batch.
An important indicator of a CNC machining supplier’s commitment to quality processes is whether they adopt a QMS (Quality Management System). A QMS is a formailsed system that documents processes, procedures and responsibilities for achieving quality objectives and outcomes.
At Penta, our QMS encompasses the planning, quality control, quality assurance, and continuous improvement of quality across the business. It is a reference point for our company wide quality standards throughout preparation, production and inspection – to ensure we deliver consistently for our customers.
Robust quality inspection processes and control measures
Perhaps the most important documented process of all – the inspection process!
A well-documented process detailing multiple inspections throughout production will ensure every component meets your exacting specifications and minimise non-conformance issues.
A comprehensive quality inspection process may look like this:
- Order review by preparation team: a dedicated preparation team reviews order specifications and drawings before machining, to ensure full comprehension of project requirements and facilitate effective preparation for machining.
- First-off inspection: following the completion of the first component, a designated inspector meticulously scrutinises it against approved drawings and specifications to verify conformity and establish a benchmark for subsequent components.
- In-process inspection agreed: collaboratively defined inspection points and frequencies ensure ongoing quality control. Early detection of deviations from tolerances allows for prompt corrective actions and maintains consistent quality throughout the batch.
- Final inspection on designated parts: a comprehensive inspection of a designated number of components (aligned with customer requirements) verifies dimensions, surface finishes, and all critical parameters before the parts are shipped.
- FAIRs and certification compliance (as required): provision of First Article Inspection Reports (FAIRs) and relevant certifications demonstrates adherence to quality requirements and ensures transparency and accountability.
Inspection methodologies
A reputable CNC machining company should have a dedicated and fully trained inspection team.
This team will closely examine components for dimensional accuracy, tolerance, surface finish, and roughness.
To do this, they should use a range of specialist equipment. Here are some of the key bits of kit we use here at Penta:
- Coordinate measuring machines (CMMs): sophisticated machines that utilise a computer-controlled probe to meticulously map the geometry of a part, capturing millions of data points to create a highly accurate 3D representation. This allows an inspector to compare the part's dimensions and tolerances against the original design with unmatched precision.
- Optical Comparators: These versatile instruments magnify silhouettes of parts onto a screen, facilitating a visual comparison against pre-defined standards and templates. This is particularly useful for inspecting complex shapes and identifying dimensional deviations.
- Visual Aids: Magnifying devices such as microscopes and lighting aids can and are used to aid in the visual inspection of materials and final components. These devices can be used to check for the presence of foreign objects, any corrosion and/or damage from the machining process.
- Surface Profilometers: Profilometers are non-contact instruments that utilise a fine stylus or laser to measure the surface roughness of a machined part. This provides a quantitative analysis of surface textures, ensuring finishes meet the precise requirements specified in your design.
Equipment calibration and tooling and machining maintenance
Maintaining CNC machines at their peak performance is crucial for consistent manufacturing quality. Reputable suppliers prioritise regular maintenance and preventive measures to uphold operational efficiency and precision.
Through proactive maintenance and vigilant monitoring, suppliers minimise downtime, prevent errors, and safeguard the integrity of their machining processes. When evaluating potential partners, feel free to request documentation of their systematic machine maintenance practices.
In addition to machine upkeep, reputable suppliers place a high emphasis on equipment calibration. Regular calibration ensures the accuracy of instrumentation, essential for delivering components with impeccable precision. Suppliers typically conduct annual calibrations to uphold the integrity of their tools and instrumentation.
As you consider partnering with a CNC machining company, don't hesitate to inquire about their calibration protocols to ensure precision and reliability in manufacturing.
Continuous Improvement
Does your CNC machining supplier or a prospective supplier foster a culture of continuous improvement?
Continuous improvement goes beyond simply meeting specifications; it’s about innovation, constantly seeking ways to refine processes, identifying areas for betterment, and ultimately, ensuring that each component produced is of the highest quality.
This is an area we are very passionate about at Penta – one of our core values is ‘striving for improvement’, so it’s in our DNA.
Here are some ways a CNC machining company should be ingratiating continuous improvement into their production process:
- Post-production analysis – otherwise known as learning from every project. By meticulously reviewing post-production data, CNC machining teams can identify areas for streamlining or optimising toolpaths. This data-driven approach ensures that each subsequent project benefits from the collective knowledge gained.
- Customer feedback – valuable feedback comes not just from internal processes, but also hearing back from purchasing managers like you. Leading suppliers will proactively seek feedback to understand how they can exceed expectations. This collaborative approach is something we’re very passionate about at Penta – ‘communication’ is one of our core pillars of service and we strive to keep open communication throughout the production process.
- Reacting to NCRs – even the most meticulous processes can encounter the occasional stumbling block. The key lies in how these situations are handled. When non-conformance reports (NCRs) arise, they should be viewed as opportunities for growth. By investigating the root cause and implementing corrective actions, suppliers can prevent similar issues from reoccurring, continuously strengthening their quality assurance systems and raising the bar for quality excellence.
Finding the right CNC machining supplier
At the heart of quality assurance lies a collaborative relationship between a buyer of machined parts and the CNC machining supplier. This should be based on transparency, communication, and mutual trust.
To find a supplier that is willing to work with you so closely, you’re going to need to do your due diligence.
You can read more about getting what you want from your CNC Machining partner in our free ULTIMATE GUIDE ebook – which gives you more tips on what to look out for when assessing the quality credentials of a CNC machining supplier:
Next steps
Here at Penta, not only are we obsessed with quality, we also love talking to prospective customers about quality. If you’d like to quiz us about our quality credentials or even arrange to come in and see for yourself, we’d love to hear from you.
Give the Penta team a call on 023 9266 8334 or email .