Hard Anodising vs. Sulphuric Acid Anodising for CNC Machined Components
25th Mar 2024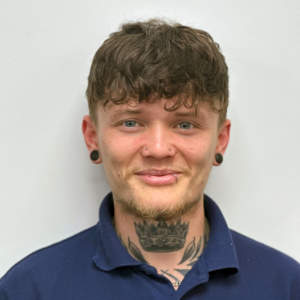
In the world of CNC machined components, the finishing touches can make all the difference. Anodising is a popular method used to enhance the surface properties of metal components, offering improved durability, corrosion resistance, and aesthetic appeal.
Among the various types of anodising processes, two prominent methods stand out: Hard Anodising and Sulphuric Acid Anodising. In this blog, I'll delve into the distinctions of each of these finishing processes, comparing their benefits, common applications, and suitability for CNC machined components.
Understanding Anodising
Before we delve into the specifics, let's grasp the fundamentals of anodising. Anodising is an electrochemical process that forms a protective oxide layer on the surface of metals, primarily aluminium and its alloys. This oxide layer not only enhances the material's surface hardness but also improves corrosion resistance and provides a base for decorative finishes.
Anodising involves immersing the metal component in an electrolytic solution and passing an electric current through it. The type of anodising process, along with variations in parameters such as voltage, current density, and electrolyte composition, determines the characteristics of the resulting oxide layer.
Anodising process – components immersed into electrolytic solution
Hard Anodising
Hard anodising, also known as Type III anodising, is a specialised anodising process that produces a thicker and denser oxide layer compared to conventional anodising methods. This results in exceptional hardness and wear resistance, making it ideal for applications requiring superior durability.
Benefits of Hard Anodising:
- Enhanced hardness: Hard anodising creates an oxide layer that is significantly harder than standard anodising, offering excellent abrasion resistance.
- Improved wear resistance: Components treated with hard anodising exhibit enhanced resistance to wear and friction, prolonging their lifespan in demanding environments.
- Corrosion protection: The dense oxide layer provides effective protection against corrosion, extending the life of the component.
- Dimensional stability: Hard anodising maintains tight tolerances and dimensional stability, crucial for precision engineering applications.
- Dielectric properties: The insulating properties of hard anodised coatings make them suitable for electrical insulation applications.
Aluminium 7075 component with a Hard Anodising finish
Common applications of Hard Anodising:
- Aerospace components
- Automotive parts
- Hydraulic systems
- Medical devices
- Defence components
Sulphuric Acid Anodising
Sulphuric acid anodising, also known as Type II anodising, is the most common form of anodising used across various industries. It produces a thinner oxide layer compared to hard anodising but offers excellent corrosion resistance and aesthetic options.
Aluminium 6082 T6 electronics housing with a soft blue Sulphuric Acid Anodising
Benefits of Sulphuric Acid Anodising:
- Corrosion resistance: Sulphuric acid anodising provides a protective oxide layer that enhances the material's resistance to corrosion, making it suitable for outdoor and marine applications.
- Aesthetic options: This process allows for a range of colour options through dyeing, providing decorative finishes along with functional benefits.
- Electrical insulation: Like hard anodising, sulphuric acid anodising offers electrical insulation properties, making it suitable for electronic components.
- Cost-effectiveness: Compared to hard anodising, sulphuric acid anodising is generally more cost-effective, making it an attractive option for large-scale production.
Common applications of Sulphuric Acid Anodising:
- Architectural components
- Consumer electronics
- Automotive trim
- Sporting goods
- Decorative items
Aluminium component with a natural Sulphuric Acid Anodising
Quick Comparison: Hard Anodising vs. Sulphuric Acid Anodising
Characteristic |
Hard Anodising |
Sulphuric Acid Anodising |
Thickness of Oxide Layer |
Thicker and Denser |
Thinner |
Hardness |
Extremely Hard |
Moderate |
Wear Resistance |
Excellent |
Good |
Corrosion Resistance |
Excellent |
Good |
Aesthetic Options |
Limited |
Wide Range (Through Dyeing) |
Cost |
Higher |
Moderate |
Common Applications |
Aerospace, Automotive, Medical Devices |
Architectural, Electronics, Sporting Goods |
Understand your options
Natural hard anodised 7075 T6 structural aluminium side support plate
It’s important to really understand the nuances of surface finishing techniques for CNC machined components. While hard anodising excels in providing unparalleled hardness, wear resistance, and corrosion protection, sulphuric acid anodising offers a balance between functionality and aesthetics, with a wider range of colour options and cost-effectiveness.
It’s also important to note that the type and grade of material used for your component can have a big impact on the anodising method you choose, not only for function but also aesthetics. For example, a clear (or natural) anodising finish on certain grades of material can result in a different colour to that on other grades, some may have a silver finish, but others may have a yellow tint. If the aesthetics of the component are critical it’s important to understand how the material grade choice will impact this.
It is crucial to speak to a trusted CNC machining supplier to better understand your options when it comes to what is best for your project – not only will it have an impact on the fit, form and function of your final component, it can have a big impact on cost.
One-Stop Solution for Anodising
At Penta Precision, we understand the significance of surface finishing in CNC machining. That's why, through our network of trusted providers, we offer a comprehensive range of finishing processes, including hard anodising and sulphuric acid anodising, to meet your specific requirements.
Penta Precision offers a seamless experience from design to delivery across a variety of sectors, so whether you require superior durability with hard anodising or aesthetic versatility with sulphuric acid anodising, we've got you covered.
If you’d like to discuss your next CNC machined component project with our team, please call 02392 668334 or book a Discovery Call with us here.