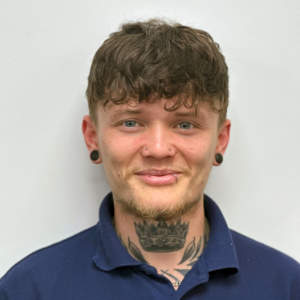
As the Lead Quality Inspector here at Penta, I see firsthand the importance of precision machining for flow measurement equipment and fluid control applications . These components must meet stringent requirements to ensure the final product operates consistently and effectively. Any imperfections can lead to big problems. Unfortunately not every machining supplier is set up to meet these high standards.
Applications and instrumentation
Flow measurement technology has a wide range of applications, including:
- Leak detection – identifying water loss from pipes or gas emissions into the atmosphere
- Fluid analysis and monitoring – detecting contaminants within fluids, identifying the fluid itself, or identifying particulates within it
- Flow rate control – including valves and regulators that precisely control flow rates.
Depending on the exact purpose of the flow analysis equipment and the technology used to interpret the data, the instruments can vary greatly in design. However, when it comes to the machined components that make up these devices, I’ve noticed some common requirements across all applications, whether it’s for liquid or gas, leak detection, particle analysis, fluid identification, or contaminant investigation.
Machining requirements
Burr-free
In my experience working with customers in this area, the most common requirement is a better-than-average surface finish, but most importantly, absolutely no burrs resulting from the machining process.
Brass flow measurement component
Why no burrs?
Many flow measurement systems use components with multiple intersecting holes. These holes allow the flow of liquid or gas and enable the measurement system to function. If there are burrs, debris, swarf, or other surface imperfections within these tubes or holes, the flow can be disturbed, leading to false data and incorrect results.
There is the additional risk of burrs becoming dislodged, which can cause further issues like blocking valves or damaging seals within the equipment. Depending on where the damage occurs, this can be very expensive to fix.
No coolant or contaminants
Another critical requirement is to ensure that components are free from any coolant, oil, or other contaminants.
CNC machine with coolant
On the face of it, producing burr-free, clean components might not seem too much to ask of a machining company. But when the quality of components impacts the performance of the final instrument, reputations are at stake.
Achieving a pristine, burr-free, ultrasonically-cleaned component manufactured to the drawing once is generally fine. Achieving it time after time, over thousands or hundreds of thousands of components - that's where challenges arise.
And with this sort of equipment, we’re not talking a simple deburr and give it a quick rub clean. These components often have complex internal structures with multiple cross holes, increasing the likelihood of burrs. Getting inside these structures to deburr and clean is tricky, requiring specialist equipment and skilled experts with plenty of experience.
Ultrasonic cleaning
Tolerance matters
Another vital aspect of machining for components involved in fluid control application is maintaining precise tolerances. Even the slightest deviation can significantly impact performance.
Components must fit together perfectly to ensure seamless operation and accurate measurements.
Maintaining these tight tolerances requires advanced machinery, meticulous planning, and a deep understanding of the application’s requirements.
Meeting tight tolerances consistently over medium to large production runs is no small feat. It demands not only modern equipment but also highly skilled machinists who can adjust and maintain the machines with precision.
How Penta meets these challenges
At Penta, we are well set up to serve this industry. We have a dedicated, skilled deburring resource for managing those hard-to-reach intersecting holes, on-site rumbling capability for a pristine surface finish, and ultrasonic cleaners to ensure all machining residue is removed, even within complex internal structures.
Rumbler
Additionally, our robust manufacturing processes and detailed inspection regime mean that we can confidently achieve the necessary quality levels every time.
Frequently we find that our customers, including those working in fluid measurement, do not inspect every component we deliver, just a sample. At the start of every quote, we agree on the inspection requirements and identify what FAIRs or other certification is needed.
Our dedicated inspectors, including myself, utilise a range of equipment, including CMM, shadowgraphs, and gauges to ensure we meet quality requirements. Over time, we’ve proved our systems work, and our customers trust our quality across all the components we make.
Quality inspection - CMM
At Penta, we want to be the manufacturing supplier you can forget about. Rely on us, and your components will arrive, on time, to specification, every time. It’s thanks to our robust processes and dedication to our three Cs across the business: Communication, Care, and Consistency. We communicate well. We take care at every stage. We are consistent in our service.
If you need a manufacturing company you can forget about, get in touch with one of our estimators to discuss your project and find out more. As someone who takes immense pride in ensuring every component meets the highest standards, I look forward to helping you achieve the same.