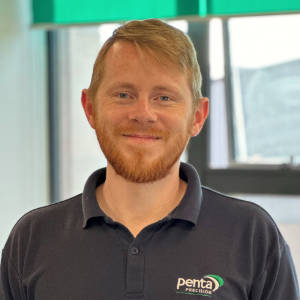
As a design engineer, I’m sure you’re all too familiar with, what sometimes feel like, opposing factors involved in component design: from competing demands around cost-efficiency, time constraints, the desire for quality and specific requirements of your application.
With so many aspects to consider, it's important to adopt best practices for design for manufacturability (DFM) early in the design process.
What is design for manufacturability (DFM)?
Design for Manufacturability commonly referred to as DFM is a key early stage of production development. It is a methodology for optimising a component’s design for the machining process.
The aim of DFM is to make a part easier and more efficient to machine and ultimately more cost-effective, without compromising on quality. It’s a careful balancing act as you incorporate time-saving aspects into your design without wanting to compromise on form, fit or function.
What aspects are considered in the DFM process?
DFM involves the consideration of various factors early in the design process. The exact process will vary between components but there are particular aspects of the design that will usually be assessed for machinability and efficiency which I outline below.
1. Material selection
The type of material, the specific grade and the size of the material can all play a significant role in the cost of a component.
Sometimes a non-standard, highly specialist and expensive grade of a material is required. On other occasions a standard plate, bar or tube of a slightly less strong/corrosion resistant/lightweight grade will do just as well for the application at half the price.
The type and grade of material selected also determines the complexity and cost of machining. For example, certain materials may require more costly, specialist tooling making it more expensive to machine overall. Getting advice with material selection early on is strongly recommended.
2. Component geometry
At times a more complex design is unavoidable – and other times simplicity is key.
Designing a component for machining involves finding a balance, and sometimes, small compromises in design can produce a more efficiently machinable part.
3. Tolerance requirements
It amazes me how often I see a drawing come through with a tight tolerance, where a more open tolerance would have been more appropriate - significantly reducing machining time and costs.
Tighter tolerances for a component geometric flatness on certain surfaces, for example, can have a particularly significant impact on the overall time and complexity of machining.
Consider another scenario: when you're machining a shaft intended for insertion into a tube, a specific tolerance becomes essential to ensure that these two components work seamlessly when assembled. If the difference in size between the two parts is minimal, a more precise tolerance becomes necessary. On the other hand, if a snug fit isn't necessary, you can opt for a smaller shaft with a broader tolerance range.
By involving an experienced CNC machining company and accessing their specialised team, you can design your part with machining considerations from the outset, rather than as an afterthought. They can help you to modify the design to make it more machinable while still retaining functionality and aesthetic requirements, ensuring a smooth transition from design to production.
Benefits of a collaborative design approach
The advantages of seeking external expertise in the early design phase are numerous. The three main benefits are:
- Enhanced manufacturability – potential manufacturing challenges can be identified early on, and design modifications made to improve efficiency and reduce production costs. For example, designing parts with easy access for tooling and fixturing also allows for faster and more accurate setups, reducing the overall production time meaning a shorter lead time.
- Reduced production delays – nailing the production process during the design stages will undoubtedly reduce the risk of delays during the machining process and increase overall efficiency. Considerations such as minimising tool changes, reducing setup times, and optimising machining paths can significantly increase production efficiency and mitigate the risk of delays from unforeseen issues.
- Cost-effective design – the design can be optimised for cost-effectiveness from day one rather than retrospectively. This may include reducing material waste, simplifying the design, and minimising the need for secondary operations – saving on materials, labour costs and production time and reducing lead times.
Who should be involved in the design process?
I recommend partnering with a CNC machining company that offers both standard machining design advice and a dedicated design-for-manufacture service.
Employing a DFM service will be an upfront investment, but one that could reduce the final production cost by up to 70%.
When you seek the expertise of an experienced CNC machined parts supplier, you benefit from a full spectrum of expertise including in-house design engineers, machining experts, production engineers, material buyers and quality control specialists.
DFM in the real world
A recent instance where the DFM process proved its effectiveness involved an enclosure intended for a security sensor installation.
The customer initially presented Penta with a 3D printed prototype and preliminary design sketches. After conducting a thorough assessment of the designs, we identified several design adjustments that could significantly enhance the enclosure's manufacturability and suitability for its intended purpose.
Through close collaboration with the customer, Penta provided recommendations to the design engineer on material selection, tolerances, application guidance, and surface finishes.
In the case of this specific enclosure, this collaborative effort and the resulting recommendations led to a production cost reduction of over 30%, all while successfully delivering a weather-resistant, secure container that was aesthetically pleasing, as per the project requirements.
Next steps
When working on your next project, involving others in the design process through a collaborative approach is crucial for achieving cost-effective design, high-quality components, and efficient production.
By leveraging the expertise and insights of an experienced CNC machining supplier, you can enhance manufacturability, improve quality, reduce production delays, and optimise your design for cost-effectiveness.
Here at Penta, we take pride in of our design-for-manufacture service.
How does Penta work?
Here at Penta, we are proud to adopt our ‘Proven Process’ at all stages of our service. This means we can deliver on our commitment to: communicate at all stages, take care with the projects placed with us and remain consistent.
What is Penta’s DFM process?
- Arrange a free initial telephone consultation with our estimation team to discuss your project and allow us to clarify your requirements. You can email us on to arrange this or give us a call on 023 9266 8334.
- We’ll then scope out the work in order to supply a quote and schedule for completion.
- Once you’ve given us the go-ahead, we’ll work on your design, liaising with you throughout. Find out more about our design for manufacture service here.
Just need a bit of advice?
We can provide that too. Machining design advice is offered as standard for all our manufacturing customers. Call our experienced engineers on 023 9266 8334 to talk through your project today.