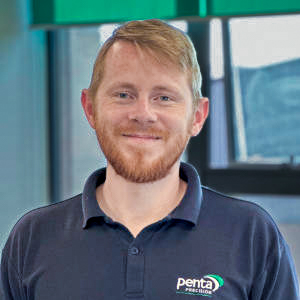
Sharp edges may seem minor, but they can create stress points that affect part reliability and lifespan. Choosing the right edge type, whether a chamfer or fillet, plays a key role in performance, safety, and efficient assembly. Small design choices like this often have big impacts in precision machining.
Below we’ll explore the differences between chamfered and filleted edges and when to use each. It explains how edge choices influence cost, machining time, fit, and appearance. You’ll also find practical tips on tooling, CAD design, and common use cases to support your decision-making.
Have a CAD or STEP file of a part with a chamfer edge? Contact our team to get a custom quote, and bring your part to life.
Key Takeway: The Difference Between Chamfer and Fillet Edges
Fillets are rounded edges that reduce stress and improve safety, making them ideal for high-load or high-contact components. Chamfers are angled edges that ease assembly and reduce machining time, often used in mating features or threaded holes. This section compares fillet vs chamfer, helps you decide which to use, and explains how each affects cost, tooling, and design.
What Is a Fillet and When to Use It
Fillets are rounded curves that smooth the transition between two connected surfaces. They’re used to eliminate sharp edges and help distribute mechanical stress more evenly. Fillets are common in high-precision components used in aerospace, medical, defence, and advanced manufacturing sectors.
High-Stress Areas
Fillets reduce stress concentration at internal or external corners where force is applied. This lowers the risk of cracks or fatigue failure in parts under constant load. Engineers use fillets in brackets, supports, and housings that need to withstand long-term mechanical stress.
Smooth Appearance
Fillets give parts a clean, curved look that feels refined and professional. They're especially popular in components where appearance matters, such as consumer products or ergonomic tools. A soft edge can also improve the surface quality of coatings or finishes.
Safe Handling
Sharp edges can be uncomfortable or even hazardous during manual handling. Fillets reduce that risk by creating smooth, touch-friendly transitions. This is important in environments where people regularly install, inspect, or service parts by hand.
Better Material Flow
Fillets help improve material flow in moulding, casting, or forming processes. By guiding material around corners more smoothly, they reduce the chance of voids or weak points. In CNC machining, they also support more consistent tool movement and wear reduction.
What Is a Chamfer and When to Use It
Chamfers are angled edges cut into a part, typically at 45 degrees, though the angle can vary. They are used to break sharp corners, ease assembly, and speed up manufacturing processes. Chamfers offer a practical balance between precision, cost, and performance.
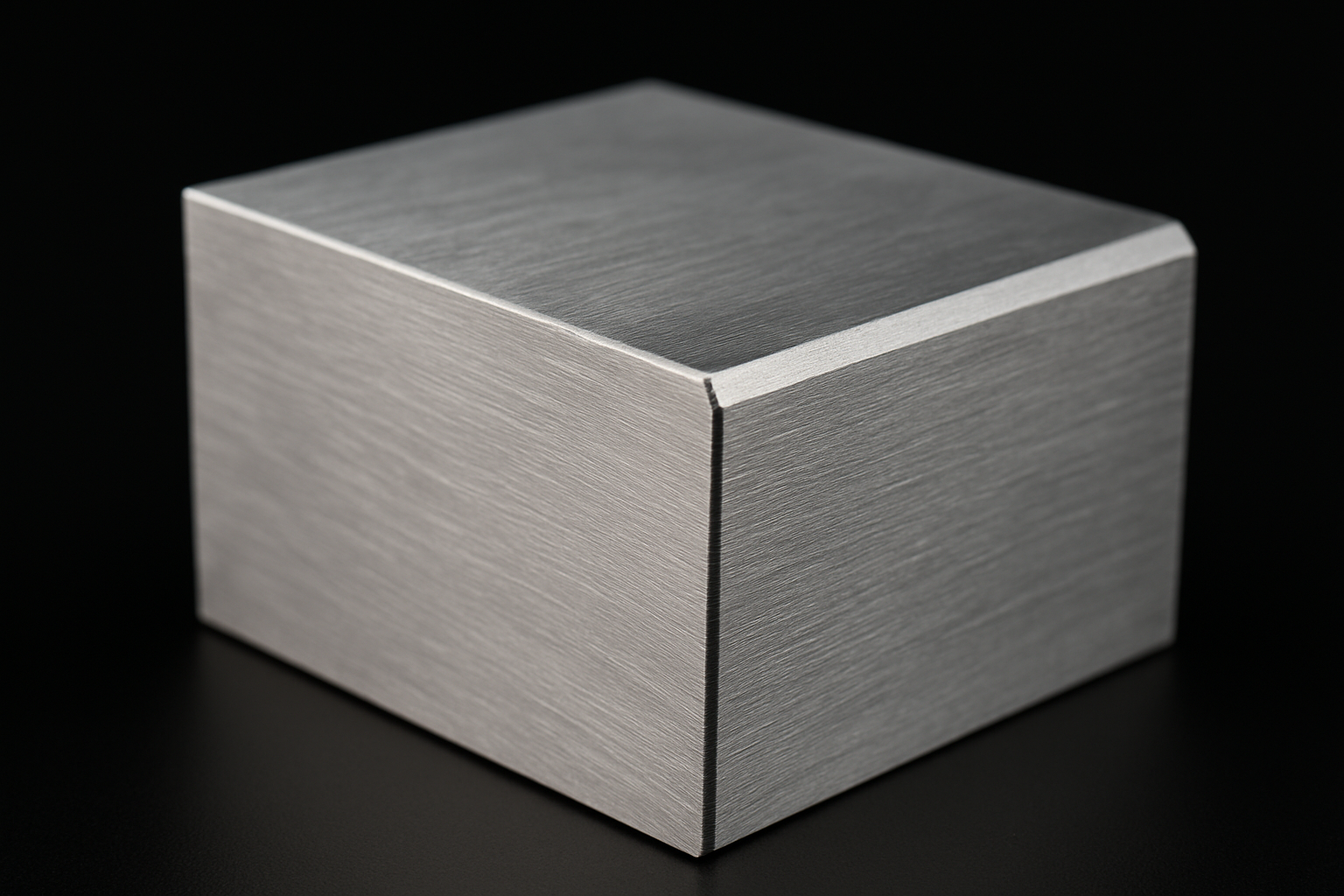
Easier Assembly
Chamfers help parts slide together more smoothly during assembly, especially when working with fasteners or mating components. They guide pins into holes, reduce jamming, and support alignment. This makes them a reliable choice for improving fit and streamlining automation.
Faster Machining
Chamfers are quicker to produce because they follow a straight path and don’t require specialised tooling. A single pass with a standard cutter is often enough to finish the edge. This saves time in machining and keeps production costs down.
Burr Removal
Sharp burrs left after machining can pose safety risks or interfere with assembly. Adding a chamfer removes the sharp edge cleanly and reduces the need for extra finishing work. This results in a safer, more efficient part right off the machine.
Functional Design
Chamfers offer a clean, technical look and help parts fit together with precision. They're especially useful in applications where sharp, well-defined edges are needed. Common examples include mechanical frames, mounting brackets, and precision enclosures.
Chamfer vs Fillet: Key Differences
Understanding the chamfer and fillet difference is essential when designing for durability, cost-efficiency, and ease of assembly. Both edge types modify transitions between surfaces, but they do so in very different ways. Your decision should reflect the part’s function, load conditions, and machining constraints.
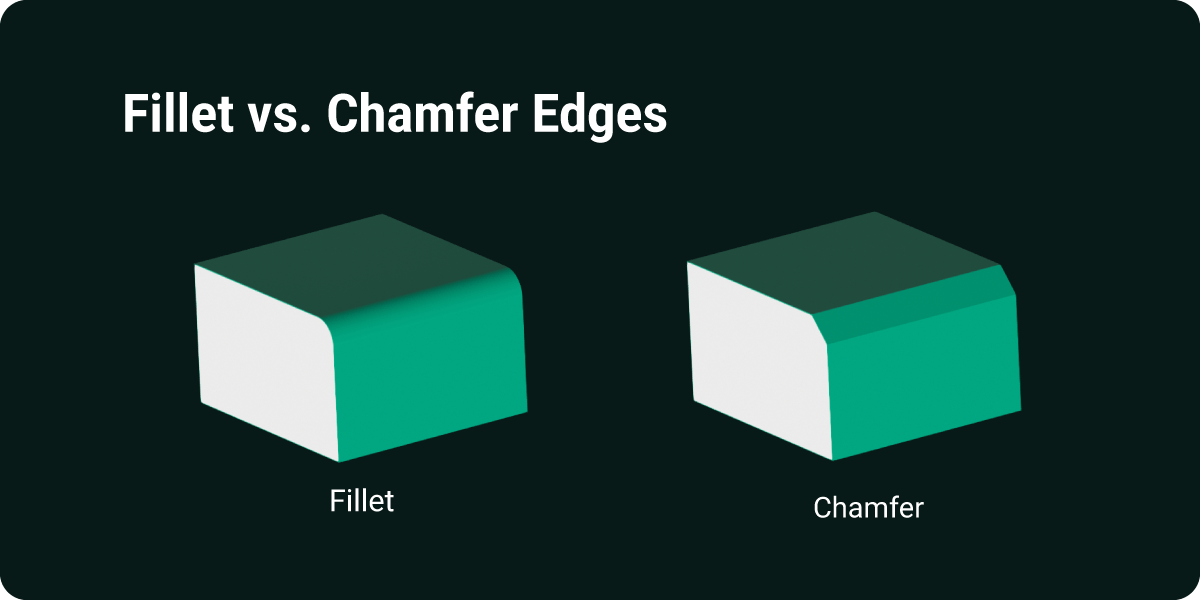
Shape and Geometry
Fillets are smooth, curved transitions between surfaces, while chamfers are angled cuts, usually straight. These differences affect how parts interact during movement, fit, or installation. Chamfers are best for guiding parts into place, whereas fillets are better for smooth motion and load transfer.
Stress Performance
Fillets perform far better in high-stress areas where force needs to be distributed evenly. Their rounded profile reduces sharp transitions, which helps avoid cracking or fatigue failures. Chamfers offer minimal stress relief and are better suited to lower-load or non-critical areas.
Cost and Machining
Chamfers are faster and more cost-effective to machine because they require fewer tool passes and standard tooling. Still, there are important considerations when machining chamfers, including angle, material type, and application needs. Fillets often need ball-end or bull-nose tools, tighter tolerances, and longer machining times. Chamfers support efficient workflows and are commonly chosen for high-volume production runs.
Appearance and Safety
Fillets provide a softer, cleaner look that’s easier and safer to handle. Their rounded nature is ideal for ergonomic parts or medical equipment where user comfort matters. Chamfers, while sleek and modern in appearance, can leave slightly sharper edges.
Assembly Fit
Chamfers are ideal for guiding parts into position, which improves fit and speeds up assembly. You’ll often see them in threaded holes, alignment features, and locating pins. Fillets can interfere with precise fits unless carefully designed with clearance in mind.
Tooling Needs
Fillets may require multiple tool passes and more specialised cutters, especially in tight or complex geometries. Chamfers, on the other hand, can be machined quickly with simple angle tools and straightforward programming. This makes them especially suitable for CNC machining services for complex parts, where speed and precision are critical.
How to Choose the Right Edge
Choosing between a fillet and a chamfer depends on your part’s performance needs, handling, and how it will be manufactured. If the part will be load-bearing, exposed to repeated force, or needs a soft edge for handling, fillets are the best fit. Chamfers are more suitable when alignment, programming simplicity, or production speed are more important than stress reduction.
Use fillets when:
- Parts are load-bearing or under frequent stress
- You need a soft, safe edge for handling
- A clean, polished finish is required
Use chamfers when:
- Parts need to align easily in assembly
- You want to simplify CNC programming
- Production speed or cost is a major factor
CAD and Machining Tips
Designing chamfers and fillets properly in your CAD model can improve manufacturing results and prevent costly delays. Fillets should have clearly defined radius values, especially where tight tolerances or internal corners are involved. Chamfers are generally easier to apply and modify in CAD, using a simple angle and depth.
The tools you select must match the edge geometry you've designed. Fillets often require ball-end or bull-nose tools and may need more than one pass to complete. Chamfers, however, are typically cut using standard tools already available in most CNC milling services, which helps streamline production.
When creating drawings or 3D models, label edge features clearly to avoid confusion during machining. Don’t assume a default edge will be applied; define chamfers and fillets as part of your design intent. This not only helps machinists interpret your specs but also ensures higher quality results with fewer revisions.
Making the Best Design Decision
Edge choices are more than cosmetic, they affect safety, functionality, and production time. Fillets add strength, reduce stress, and make parts safer to handle, which can be essential in critical components. Chamfers simplify machining and improve fit, making them ideal for high-volume or automated assembly.
Many successful designs use both edge types to meet different needs within the same part. You might add fillets inside cavities or along touchpoints while using chamfers on mounting holes or entry points. Working with experts through machining drawing services can help ensure the right balance of form, fit, and function from the start.
A thoughtful edge design saves time during machining and adds long-term value to your parts. It also makes your components easier to assemble, inspect, and use across different environments. Whether you're managing tight tolerances or optimising production, the right edge choice makes all the difference.