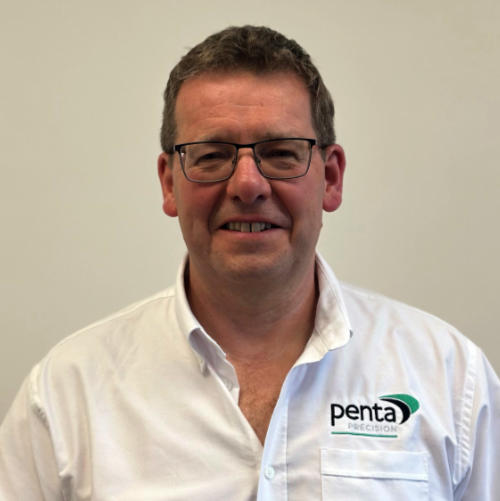
In the realm of manufacturing and design, data sheets play a crucial role in providing essential information about materials, especially when you consider that there are hundreds of thousands of material grades on the market.
When it comes to CNC machining, data sheets are often relied upon by designers to guide their decision-making process. Looking at a searchable database of materials properties like MatWeb can be useful for narrowing down your choice and ruling out certain materials or grades as unsuitable.
However, it’s important to recognise that data sheets have their limitations, particularly in the context of designing components for CNC machining. Data sheets represent the average of lab-test figures, not the full range of real-world performance. In this blog post, I’ll explore these limitations in more detail, discuss why designers should approach data sheets with caution and perhaps most importantly, outline how you can overcome the limitations.
But first, let’s make sure we’re on the same page…
What information can you expect from a data sheet?
A data sheet should provide comprehensive information about a grade of material, and in particular its properties including: physical, mechanical, electrical, thermal, optical, descriptive and processing properties. Sometimes they will offer characteristic notes and chemical composition.
Now let’s look at the main limitations…
Material Variability
Data sheets provide average or typical material properties, but they don’t account for the inherent variability in materials. Variations in hardness, grain structure, and other material characteristics can significantly influence the performance of the finished component within an application.
Plastics are particularly challenging and there are a wide range of factors that affect performance including temperature and humidity as well as stress and strain. Not only that, but these factors will take effect in different ways over different periods of time. This means that understanding how a particular plastic will react to its environment, and the implications for the overall lifespan of the part, can be a complicated matter.
Designers must also be aware that relying solely on data sheets may lead to unexpected challenges during CNC machining due to material variations that are not adequately addressed in the provided information.
Lack of Machining-Specific Information
Data sheets typically focus on general specifications and properties of materials, but they often lack detailed machining-specific information. CNC machining involves intricate processes such as tool selection, feeds and speeds, and fixturing considerations, all of which have a direct impact on the final product. Unfortunately, data sheets rarely provide guidelines or recommendations tailored specifically for CNC machining applications, making it challenging for designers to optimise their designs for the manufacturing process.
Limited Geometric Considerations
CNC machining encompasses a wide range of geometric complexities, from simple shapes to intricate designs with intricate features. Unfortunately, data sheets often fail to provide guidance on the manufacturability of specific geometric features. Designers may encounter issues related to tool accessibility, undercuts, or thin walls that data sheets may not address adequately. Consequently, relying solely on the data sheet can lead to costly design iterations and compromises on the desired component functionality.
Incomplete Tolerance Specifications
Tolerances are critical in CNC machining, as they determine the permissible variation from the intended design dimensions. While data sheets may provide general tolerance guidelines, they often lack the precision necessary for designing CNC machined components. Each machining operation, such as milling or turning, may have different tolerance capabilities that are not adequately communicated in the data sheet. Without a thorough understanding of machining tolerances, designers risk creating designs that are either overly conservative or prone to manufacturing errors.
Insufficient Surface Finish Information
Surface finish is a crucial aspect of CNC machining, affecting not only the aesthetic appeal but also the functionality and performance of a component. Unfortunately, data sheets tend to provide limited information regarding achievable surface finishes for specific materials and machining processes. Designers may be left guessing the appropriate surface finish requirements, potentially leading to suboptimal results or the need for additional post-machining processes to achieve the desired outcome.
How can you overcome the limitations of data sheets?
Research for multipoint data
Data sheets should be one tool in your research toolkit. If you want to know how a material will perform in your application, you’ll need to undertake further research for multipoint data – performance over a range of temperatures, over time, and so on. Some materials suppliers will provide these, and you can often find further information online.
Testing, testing…
If you’re in the early stages of product development, it’s a good idea to conduct testing yourself once you’ve narrowed down your options.
There are so many variations in application that the final step always needs to involve your own R & D. Conduct testing yourself, under the spectrum of conditions you expect in the finished product. This will ensure you’ve considered a range of properties which should include at least the following:
- Impact resistance
- Modulus (stiffness)
- Creep (deformation over time)
- Thermal properties
- Anisotropy (varying performance along different axes).
Find a machining partner, not just a supplier
It always pays to partner with a trustworthy CNC machining supplier. It’s not enough to do your own research and testing of a material for your application. You also need to ensure you have selected a material grade that is suitable for machining and takes into account your budget. Some material grades are inherently more difficult to machine, and therefore take longer and ultimately increase the cost of machining your part.
A competent CNC machining company should take the time to understand your part and its application, and provide expert guidance on material selection based on the specificities of the CNC manufacturing process.
Conclusion
While data sheets serve as valuable references for designers, they have significant limitations when it comes to CNC machined component design. I urge designers to approach data sheets with caution and understand that additional considerations specific to CNC machining are necessary.
Collaborating closely with an experienced CNC machining supplier, conducting iterative prototyping, and leveraging real-world testing can help overcome the limitations of data sheets and ensure the successful design and manufacturing of high-quality CNC machined components.
By combining the information provided by data sheets with hands-on experience and seeking external expertise with regards to the machining process, designers can achieve optimal results and avoid potential pitfalls.
Next steps
If you’ve read this blog and thought, where can I find a CNC machining company who won’t just fire back a quote without question, but will take the time to understand my needs and offer bespoke advice, you’re in the right place.
Here at Penta Precision, we are a true manufacturing partner. If you’d like to have a no obligation consultation with us about your next project or component, please call the Penta team on 023 9266 8334 or make an enquiry here.
I'd also love to connect with you on LinkedIn