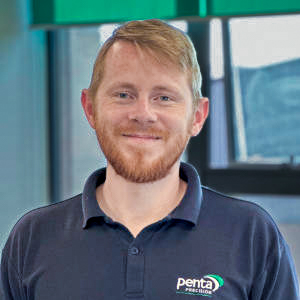
Medical-grade stainless steels are vital materials in healthcare, where performance and safety are non-negotiable. Choosing the right grade affects not only the function of your parts but also your production costs and regulatory compliance. The right decision early in your design process can save time, reduce risk, and ensure better outcomes for patients and users.
Understanding your options, especially around 316L surgical steel, ensures your medical designs are safe, reliable, and fit for purpose. You need to balance factors like corrosion resistance, machinability, and biocompatibility to get the best results. In this guide, you will learn how 316L and other medical-grade stainless steels compare for different applications.
Want to get in touch with our team to discuss your project?
What Is Medical-Grade Stainless Steel?
Medical-grade stainless steel refers to a category of stainless steels that meet strict safety, biocompatibility, and corrosion resistance standards. These materials are used for implants, surgical instruments, and support devices where hygiene and durability are essential. The properties vary between grades, depending on their alloy compositions and intended applications.
Is Surgical Steel the Same as Stainless Steel?
You may wonder, is stainless steel and surgical steel the same? Surgical steel is a subset of stainless steel engineered specifically for medical use. Its chemical makeup offers higher corrosion resistance and lower nickel release compared to standard industrial stainless steels.
When 316L Surgical Steel Is the Right Choice and When It's Not
316L surgical steel is often the first material engineers consider for medical device manufacturing. Its low carbon content, excellent corrosion resistance, and biocompatibility make it ideal for critical applications. However, it is not always the only or the best option depending on your project needs.
Other medical-grade stainless steel types may offer better machinability, lower cost, or more suitable performance for non-body-contact components. You need to weigh the specific requirements of your design carefully before committing to 316L. Understanding the alternatives can help you find the right balance between quality, cost, and manufacturing efficiency.
But it is easy to see why 316L remains the ‘go-to’ choice for many healthcare-related projects. It consistently delivers the strength, reliability, and patient safety demanded by high-performance medical equipment. Let’s explore why 316L surgical stainless steel remains trusted by manufacturers around the world.
Use 316L Surgical Stainless Steel for Body-Contact Applications
You should consider specifying 316L surgical steel if your product is going to touch any part of the human body. Its metallurgical composition makes it a low-allergy material, trusted across healthcare sectors. The ‘L’ refers to its low carbon content, which improves its corrosion resistance against body fluids and cleaning agents.
AISI 316L (WNR 1.4404/UNS S31603) is an Austenitic stainless steel known for being non-magnetic. This means it will not interfere with sensitive instrumentation, scanners, or implants. Its chemical composition is carefully controlled to maximise durability and safety.
The main elements include Carbon (0–0.035%), Chromium (16–18%), and Manganese (0–2%). It also contains Molybdenum (2–3%), Nickel (10–15%), Phosphorus (up to 0.045%), Silicon (up to 1%), and Sulphur (up to 0.03%). Together, these enhance corrosion resistance, ductility, and overall performance under medical conditions.
316L surgical stainless steel offers excellent formability, allowing tight bends and complex component designs. Despite its excellent mechanical and anti-corrosive properties, it is not the most expensive stainless steel. However, it is pricier than grades like 303 or 304, which may be suitable for non-body-contact parts.
Here’s how prices compare for a 25mm x 1,000mm section of stainless steel round bar (approximate figures):
- 17-4PH/AMS5659/H1025 – £67.00
- 15-5PH/AMS5643/H1150 – £65.00
- 440 – £63.00
- 316/316L – £23.00
- 304 – £14.50
- 303 – £13.50
316L also requires more effort to machine compared to 303 or 304, especially when milling complex features. Labour times and machining costs can increase because of the material's toughness and work-hardening tendencies. Compared to aluminium, 316L can take at least twice as long to machine.
Why 316L Is Trusted in Medical Applications
316L surgical stainless steel is trusted because it offers the ideal balance of corrosion resistance, strength, and biocompatibility. Its performance under sterilisation cycles and exposure to bodily fluids makes it reliable for long-term use. Medical manufacturers prefer it for ensuring patient safety and regulatory compliance without compromising on mechanical performance.
316L is non-magnetic, critical for applications involving scanning equipment like MRIs or other sensitive diagnostics. It resists pitting and cracking even in aggressive environments, including high-saline or chlorinated atmospheres. You can depend on its stability, even when the medical device must endure repeated stress and sterilisation.
Choosing a reliable grade like 316L surgical stainless steel protects you against future liability risks. Failures in medical components can be catastrophic, which is why standards like ISO 5832 specify 316L for implants. This level of trust has made 316L a global standard for high-risk medical designs.
Typical Use Cases for 316L Surgical Steel
316L surgical steel is widely used for orthopaedic implants such as bone screws, pins, and plates. It also features heavily in cardiovascular implants like stents and replacement heart valves where biocompatibility is critical. Surgical instruments, dental tools, and even body piercing jewellery rely on 316L for its low-allergy and high-durability properties.
You will also find 316L used in medical device housings and casings that must withstand cleaning chemicals. Devices like infusion pumps, monitoring equipment, and operating room instruments often specify 316L components. For applications involving direct body contact or repeated sterilisation, 316L remains the first-choice material.
Working with specialists in CNC stainless steel machining ensures your 316L parts meet the tight tolerances required. Precision machining for medical equipment demands control, quality, and consistency throughout the process. Partnering with the right team helps you turn 316L's advantages into manufacturing success.
303 vs 304/304L Stainless Steel
AISA 303 (WNR 1.4305/UNS S30300) and AISI 304 (WNR 1.4301/UNS S30400) are also Austenitic and so offer the same advantages as 316L but have a hint of magnetism.
You would not specify them for body-contact applications, but they would be suitable for components such as frames, bases, brackets, bodies or guards. They offer excellent corrosion resistance for indoor applications. But they may, over time, show signs of tarnish or pitting in outdoor applications or in environments with aggressive cleaning regimes.
303 has a higher carbon (0-0.15%) content than 316L (C: 0 to 0.035%) and less molybdenum (0-1%), making it less resistant to corrosion than 316L. It is also likely to have less nickel (8.00-10.00%) which is added to stainless steels to make them more ductile and formable.
303 remains the most readily machinable stainless steel because of its sulphur content. It is excellent for moving parts. 303 is available at Penta only in round bar diameters.
304 is the most utilised stainless steel in the world. It has a minimum 18% chromium content and a minimum 8% nickel content. This is the standard ‘18/8’ that you find in kitchen sinks, cookery pans, utensils and cutlery because it can withstand the acids in fruit and other foods.
AISI 304L (WNR 1.4306 or 1.4307/UNS S30403) offers better corrosion resistance than 304 because it has a lower maximum carbon content:
- 304 - 0.08%
- 304L - 0.03%
Like 316 grade, 304/304L are readily available in round bar, sheet and plate. Some limited sizes are available in square or rectangular wrought bar (along with tube, angle and channel sections).
Differences in Composition and Machinability
303 stainless steel contains higher carbon and added sulphur to improve machining characteristics. This makes it faster and easier to machine compared to 304 and 316L, saving you production time. 304, meanwhile, balances corrosion resistance and formability, making it the most widely used general-purpose stainless steel.
When to Choose 303 or 304/304L
You should choose 303 if your part demands frequent machining and dimensional precision without concern for extreme corrosion exposure. 304 and 304L are better suited when you need improved corrosion resistance, such as in structural or aesthetic components. Both materials are cost-effective alternatives when body-contact or critical biocompatibility is not required.
440B vs 440C Stainless Steel
AISI 440B (WNR 1.4112/UNS S44003) and AISI 440C (WNR 1.4125/UNS S44004) are Martensitic so they can be heat treated and hardened but have less resistance to chemicals than Austenitic stainless steels.
440 is often referred to as ‘razor blade steel’. It is used for dental and surgical instruments, heavier duty cutting blades, punches, dies and other tooling applications. Its high resistance to heat and corrosion also makes it a good choice for applications such as bearings and valve seats.
But 440 has a high carbon content compared with 316L (0 to 0.035%). The B and C in 440’s AISI number refer to the amount of carbon in each steel:
- 440B - 0.75 to 0.95%
- 440C - 0.95 to 1.20%
This high carbon content increases hardness (but reduces corrosion resistance). And this toughness can make 440 more difficult to machine (though it can be good to machine in its annealed form).
Heat-treatable steels such as 440 take longer to machine because of their hardening abilities. When heat treatment and machining to fine tolerances are part of the application, care must be taken with shrinkage allowances to ensure limits are maintained with consistency.
440B and 440C are commonly stocked in round bar and plate.
Want to learn more about machining 440 stainless steel?
Find out more about machining 440 stainless steel
Key Properties of 440B and 440C
440B contains slightly less carbon than 440C, offering a balance between toughness and hardness. 440C, with higher carbon content, delivers exceptional hardness, ideal for precision cutting edges. Both grades require careful machining allowances due to potential shrinkage after heat treatment.
Applications in Surgical Tools and Cutting Edges
You will commonly find 440 stainless steels in surgical scissors, dental instruments, cutting blades, and punches. Their wear resistance and ability to maintain sharp edges make them a smart choice for demanding medical tools. They are also used for valves, bearings, and structural parts where mechanical durability matters.
420 Stainless Steel
AISI 420 (WNR 1.4034/UNS S42000) is a medium-carbon Martensitic stainless steel widely used for medical, surgical and dental instruments, knives, cutlery, hand tools, pump shafts and plastic moulds. It is adapted for mirror polishing.
420 provides good strength and reasonable impact resistance. Its corrosion resistance is lower than the common Austenitic grades. 420’s (anti-corrosion) chromium content is 13% – not as high as 316L (16-18%). 420 is magnetic in both its annealed and hardened conditions.
It can be supplied pre-machined to reduce machining time. 420 is a good stainless steel to machine thanks to the addition of sulphur (up to 0.03%). It is usually stocked in round bar, sheet and plate.
17-4/17-4 PH vs 15-5/15-5 PH Stainless Steel
Both types of stainless steel are annealed and then age-hardened at a single low temperature to reach different temper conditions. As this treatment is carried out at a low temperature, no distortion occurs and there is only superficial discolouration. Several temper conditions are stocked to suit the required properties for differing component applications. The grades are readily available only in solid round bar format.
17-4 and 17-4 PH (AISI 630/WNR 1.4542/UNS S17400) are Martensitic stainless steels. They are hardenable, offer high wear resistance and good anti-corrosion properties. However, they are magnetic: 17-4 PH more so than 17-4 because it contains more ferrite.
17-4 PH is the most widely used of all the stainless steels that have been precipitation-hardened to increase their strength.
This stainless steel has a higher tensile strength and impact toughness, making it a key alloy for a wide number of aerospace, nuclear, oil and gas industry applications. It is a good choice for critical components that have to support heavy loads or withstand other strong forces.
Find out more about machining 17-4 and 17-4 PH
15-5/15-5 PH (WNR 1.4545/UNS S15500) is suitable for intricate parts (requiring machining) where distortion in conventional heat treatment presents challenges.
Like 17-4 grade, 15-5’s high strength and corrosion resistance make it the stainless steel of choice for aerospace applications such as landing gear components. Demands in the nuclear, oil and gas sectors also make it a common choice. Other applications include valve parts, gears, shafts, fittings and fasteners.
15-5 is precipitation-hardened but is tougher than 17-4. Specify 15-5 for applications that require higher corrosion resistance and better transverse strength properties than other Martensitic stainless steels.
Find out more about machining 15-5 stainless steel
Machining Stainless Steels For Medical Equipment
Machining stainless steels to the tolerances, quality levels and consistency required by medical device OEMs requires high levels of expertise and experience. This is usually why customers call Penta – to solve issues that have arisen with other suppliers.
Tool wear is usually higher when machining stainless steels (especially the hardened grades). Milling tends to be more challenging than turning – and tool ‘push off’ is a greater factor in the machining process. Good inspection practices are needed to ensure consistent quality outcomes.
Mechanical Properties and Corrosion Resistance
Medical-grade stainless steels offer a variety of strength and corrosion resistance profiles depending on their intended use. Austenitic grades like 316L resist pitting and cracking better, while Martensitic grades provide higher hardness but lower corrosion resistance. You must match your material selection to both the mechanical and environmental demands of your design.
Where These Grades Are Used in Medical Design
You will see Austenitic grades in implants and long-term surgical tools due to their biocompatibility and corrosion resistance. Martensitic grades dominate cutting tools, needlepoints, and dental instruments where edge retention is critical. Understanding the 316L stainless steel material properties ensures you choose the right solution for both patient safety and performance.
Get Penta Involved
Penta Precision is ISO 9001:2015 accredited for quality assurance. Our experienced engineers can help you to solve your design and engineering issues before they become expensive and time-consuming.
Depend on Penta to maintain quality and consistency through our three core values:
- Experts with Passion
- Exceptional Quality, Every Time
- Building Effortless Partnerships
For complex jobs like CNC stainless steel machining, we are trusted by medical OEMs across the UK. Our focus on collaborative partnerships ensures your project stays on track from prototype through to production. You can rely on us for superb quality, on-time delivery, and responsive service.