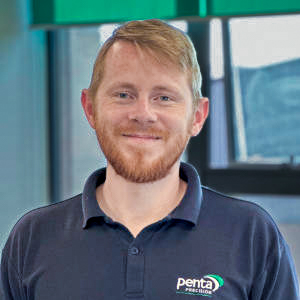
Additive and subtractive manufacturing are two of the most important methods used to create parts today. As technology advances, more businesses are comparing these approaches to find the best fit for their projects. The choice you make can influence your lead times, costs, and design flexibility.
In this guide, you'll learn how these manufacturing methods differ and when to use each one. We'll cover accuracy, materials, finishes, speed, and scalability so you can make confident, informed decisions. Whether you're developing a prototype or managing full-scale production, this guide is here to help.
Want to chat to a member of the team about our subtractive manufacturing capabilities?
Get in touch to speak with the team
What is Subtractive Manufacturing?
Subtractive manufacturing removes material from a solid block to create your finished part. It usually involves CNC machines like mills, lathes, or drills, all guided by computer programs. This method is widely used for high-precision components across industries such as aerospace, medical, and defence.
You begin with a CAD model, which tells the machine exactly where and how to cut. Subtractive manufacturing supports a wide range of materials, including aluminium, stainless steel, and engineering plastics. For the best results, go with professional CNC milling services to ensure you get the needed support from design to delivery.
Common subtractive manufacturing methods include:
- CNC milling and turning
- Electrical discharge machining (EDM)
- Laser cutting and waterjet cutting
- Grinding and polishing
These subtractive manufacturing methods are widely used across industries where strength, precision, and reliability are essential. Choosing the right method depends on your part’s geometry, material, and required finish. Each method offers different advantages depending on complexity and batch size.
What is Additive Manufacturing?
Additive manufacturing creates parts by building them up layer by layer from a digital design. Often referred to as 3D printing, it’s a popular method for prototyping, product development, and creating lightweight, complex structures. It’s especially useful when you want to move quickly from design to physical part without heavy tooling.
Common materials include plastics, resins, and metal powders, offering a mix of flexibility and strength. Once the print starts, minimal supervision is needed, making it ideal for streamlined workflows. Some parts may require post-processing like cleaning, curing, or sanding, depending on the material and application.
Popular additive technologies include:
- Powder bed fusion and binder jetting
- Material extrusion (FDM) and sheet lamination
- Vat photopolymerization and material jetting
Additive vs Subtractive: Key Differences at a Glance
Additive and subtractive manufacturing use opposite approaches to achieve the same goal, creating precise, functional parts. Choosing between additive vs subtractive manufacturing depends on part complexity, material, and the stage of your production. Each has its place depending on your design needs, materials, and production scale.
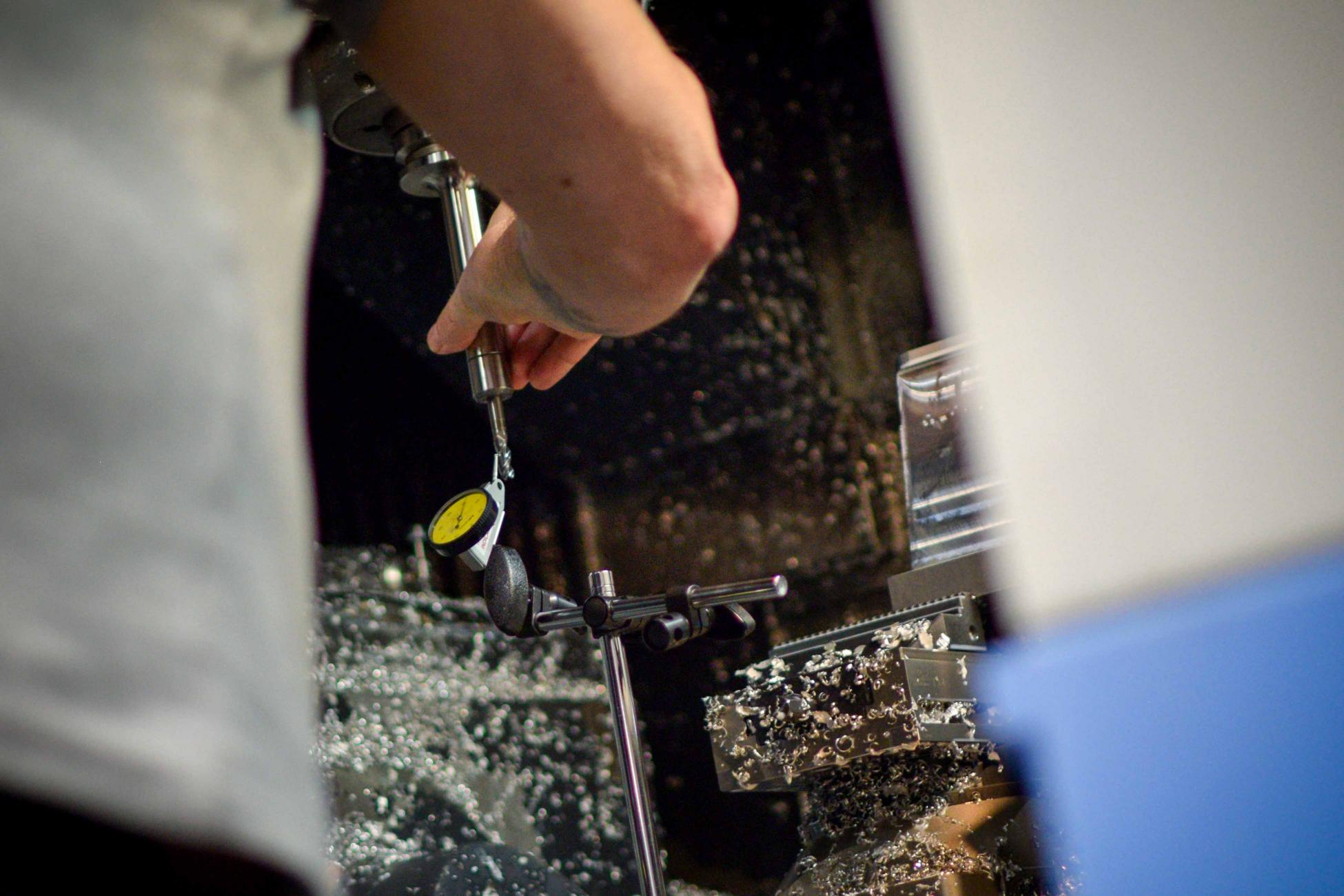
Subtractive manufacturing removes metal from a billet to create a part, producing swarf like the metal fragments shown above
Accuracy and Tolerances
Subtractive manufacturing is known for its tight tolerances, often reaching ±0.001 inches. That level of precision is critical when parts must fit together or meet industry-specific standards. Additive manufacturing usually offers tolerances around ±0.004 inches, making it better for prototypes or non-load-bearing parts.
CNC machines are great at repeating those tight tolerances, even over large production runs. Additive methods can vary depending on the machine, material, and settings used. In an additive manufacturing vs subtractive manufacturing comparison, subtractive remains the benchmark for accuracy.
Typical tolerance ranges include:
- CNC machining: ±0.001"
- SLA/SLS printing: ±0.003"–0.006"
- FDM printing: ±0.01" or more
Materials and Waste
Subtractive manufacturing supports a huge range of materials, from hard metals to engineering plastics and composites. The trade-off is material waste since parts are carved from larger blocks. Additive manufacturing is more efficient and generates far less scrap.
Additive materials are mainly plastics and select metal powders, but more options are emerging as technology evolves. Subtractive gives you broader compatibility, especially for parts needing strength and durability. You'll want to consider both material availability and performance needs.
Examples of subtractive materials are:
- Aluminium, stainless steel, titanium
- Acrylic, PTFE, nylon
- Glass, stone, carbon fibre
Surface Finish and Post-processing
Subtractive parts typically come off the machine with a smooth, consistent surface that often needs little finishing. This makes it ideal for customer-facing parts or assemblies with tight fits. Additive parts, on the other hand, usually need sanding, coating, or curing to get a clean finish.
Layer lines are common in 3D printing, especially with FDM printers. Post-processing can enhance the part’s appearance and durability, but it adds time and cost. If finish and visual quality matter, subtractive manufacturing usually comes out on top.
A helpful rule of thumb is to use subtractive for visible or high-performance parts, and additive for early design models or mock-ups. This approach saves time without compromising quality. It also allows you to test ideas quickly before moving to final production.
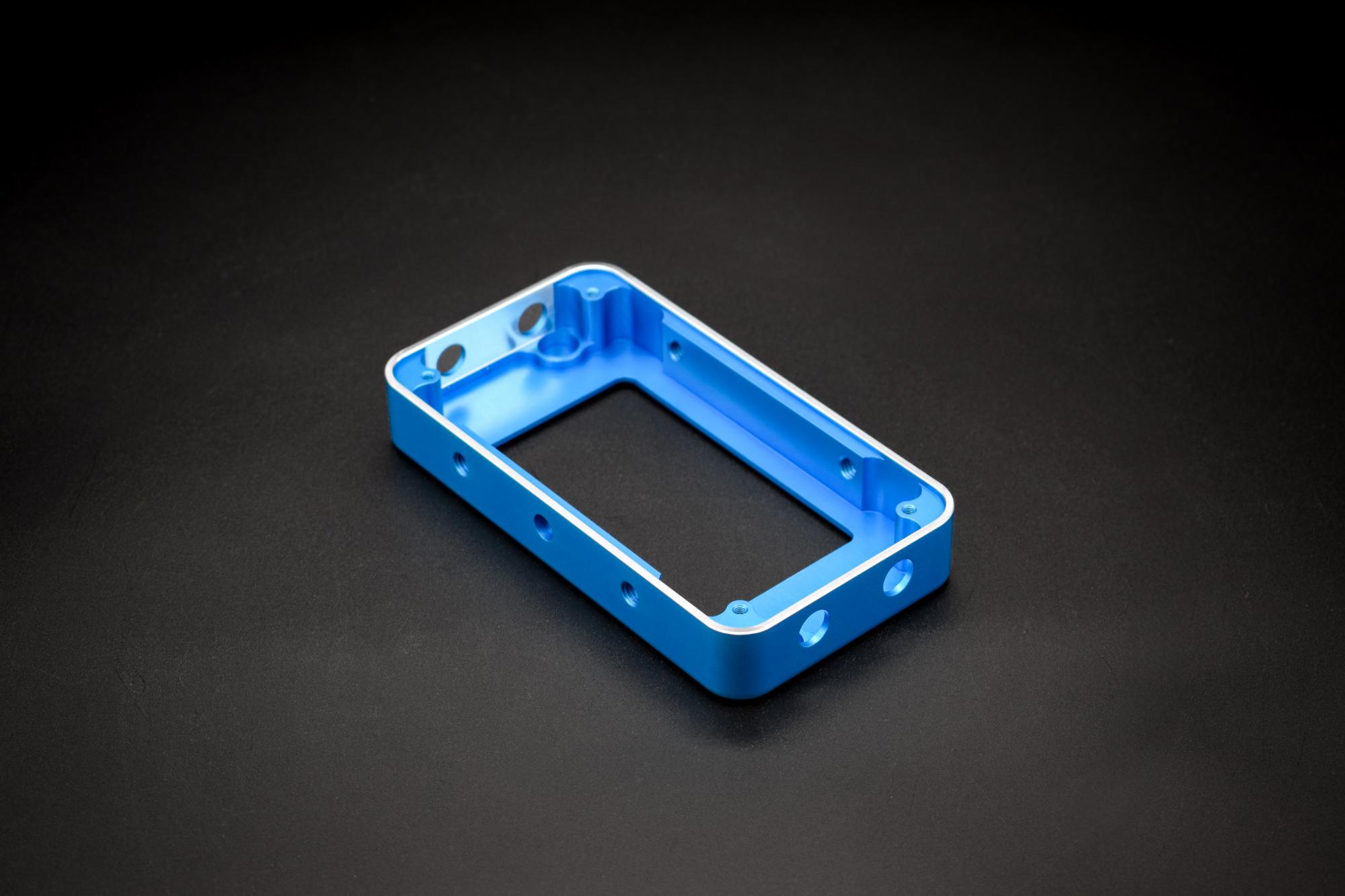
An example of a subtractive manufactured part with an anodised finish
Speed, Cost, and Scalability
Additive manufacturing shines when you're making just one or a few parts quickly. You can go from CAD to physical part with almost no setup, which is great for rapid prototyping. That makes it easier to test and tweak designs on the fly.
Subtractive manufacturing becomes more efficient as volume increases, especially with automation and multi-axis machines. When speed and scale matter, it’s the better long-term investment. Our CNC turning service shows how subtractive manufacturing can deliver precision and speed at scale.
Use additive when:
- You need a fast prototype
- You’re working in low volumes
- Design changes happen often
Design Flexibility
Additive manufacturing gives you the freedom to design features that would be impossible to machine. You can print parts with internal channels, curved structures, or moving joints in one build. That’s why it's so valuable in industries like aerospace, medical, and consumer products.
Subtractive is more limited by tool access and geometry, though 5-axis machines expand what’s possible. It’s still best for parts that need tight tolerances or functional strength. In many cases, combining both processes gives you the best results.
Great hybrid use cases are:
- 3D print the base shape
- CNC machine threads or holes for precision
Use Cases for 3D Printing vs. CNC Machining
Each method has its sweet spot depending on what you're building and how many parts you need. From quick-turn prototypes to high-volume, high-strength components, your decision should consider performance, finish, and cost. Understanding when to use each process helps you avoid delays and unnecessary expenses.
When to Use Each Process
Additive manufacturing is a great choice when you're designing intricate, low-load components. It’s ideal for quick iterations, helping you test and refine designs without the cost of tooling. It also works well for producing small batches with minimal material waste.
Subtractive manufacturing is the better option when your part needs to handle stress, high temperatures, or challenging environments. It's also preferred when you need tight tolerances and durable materials for long-term use. If you're moving into full-scale production, subtractive gives you the consistency and speed you’ll rely on.
Still not sure how or which to choose? Check out our complete guide to CNC machining for more insights. It’s a helpful resource for understanding how to evaluate additive vs subtractive manufacturing based on your project’s performance, budget, and volume needs.