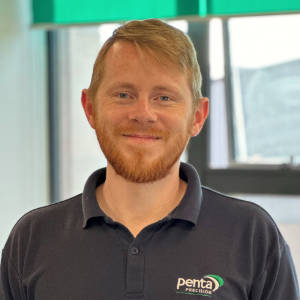
2021 has marked a year of change at Penta. From new employees to new locations, our focus for the year has been the same as ever – providing an exemplary service for customers. It feels rather indulgent to publish a blog just about Penta… but then again, not every year is like 2021. So here it is: our year in review.
January
The UK in January 2021 was not a happy place on the whole. Christmas had been ‘cancelled’, we were knee-deep in a second wave of Covid-19 infections, and into our third national lockdown. At Penta, we were working from home as much as possible, with office staff mostly remote (and fighting with unstable network connections), while the workshop team were carefully carrying on, with masks, handwashing, and physical distancing restrictions. Business continued.
Pre-Covid, lots of machines and an expanding team in a smallish location was already a challenge, but the need for physical distancing brought by the pandemic really highlighted our predicament. The decision was made to move the office staff from our head office at Aspen House into a new unit – conveniently next door to our Turning team, who were (less conveniently) already located a few minutes down the road at Portsmouth Enterprise Centre. This gave us the space to work safely in the office in person, when restrictions allowed. Penta was now operating over three locations.
February
February is the end of our financial year, and despite all of the disruption from Covid, 2020-2021 was a record breaking year for Penta. We had achieved record turnover, were set up well for the future, and with a pathway out of lockdown on the horizon, we set the ambitious target of back-to-back record breaking years.
March
The financial year started well – our forward order book was double what it was 12 months previously. Covid has been a horror: for individuals, for businesses, for the world. And yet, Penta had survived and was continuing to grow. Penta’s business strategy is purposefully built on a platform that allows the business to thrive through chaos. Covid and multiple lockdowns has been the hardest test yet, but so far, one that we have passed.
April
As the Ever Given blocked the Suez Canal in late March, by the start of April, we were feeling the knock on effects. Raw materials had been delayed, and we were seeing the start of some significant price rises. You’ll see this theme crop up again later…
May
At Penta, our presence in the medical sector was continuing to grow. Our detailed understanding of this industry and its very precise requirements means that we are able to continually delight our customers in the sector with the service that we provide. Saying that we take care with the orders placed with us isn’t just lip service. Across the business, the Penta team truly care about the work going through, and it is this that sets us apart from our competition.
June
Working across three separate sites was becoming more than just a nuisance, and with our ambitious growth targets, we knew we would soon outgrow our premises once again. It was time to get serious about moving, and with a suitable commercial property newly available in Portchester, just 10 minutes away from our main site in Portsmouth, we took the plunge and began defining the spec for our new unit.
July
As the UK lockdown ended, the subsequent ‘pingdemic’ hit, and worker shortages led to supply chain issues, laying the foundations for more raw material sourcing issues and price rises. Meanwhile, the leadership team signed off on the new unit, and work began on creating Penta’s new home, Unit 9 at Murrills Estate in Portchester.
August
While the country enjoyed (endured?) their rainy summer staycations, there was no dip in the economy’s requirements for machined components. As plans were being made for fitting out the offices, canteen, workstations and inspection department at Unit 9, across our three current sites we were as busy as ever, and simultaneously forecasting ahead to prepare for a couple of days of downtime while the machines were decommissioned, transported and recommissioned.
It was tougher than a 1,000 piece 3D jigsaw, but thanks to some very detailed planning by our Milling, Turning and Inspection Team Leaders, our Production Lead, and the Estimator team, we were able to schedule ahead the necessary gap for the move, and deliver all the work we had scheduled.
September
By September, preparation for the big move was well advanced. At Unit 9, the move team worked long hours building office furniture, managing new machine deliveries, finalising plumbing and electrics, getting the IT set up, and a million other things that needed to be done before we could move in.
Back at Aspen House and Unit 1 & 3 at Portsmouth Enterprise Centre, the team worked some long hours to ensure we would hit all our deadlines while also beginning to pack up and sort out so we’d be ready to go.
October
Friday 1st October was moving day, and the Penta team dedicated the weekend to ensure the offices and factory were ready for business to restart bright and early on Monday 4th October.
The move was a great success, with the team finally being back under one roof together for the first time in four years. In addition to the productivity and efficiency gains of having everyone on one site, three new machines were commissioned to further expand Penta’s capability and capacity: our first 5-axis milling machine, a larger format milling machine, and a new profile projector for our Inspection team.
October also saw another round of raw material price rises. Over the past 12 months, we’ve seen the cost of some materials rise by up to 150%, and at various times the fluctuation of prices has been near-impossible to manage. Availability combined with energy prices resulted in our materials suppliers’ quote lead times plummeting, and we were forced to quote and requote on jobs as the materials chaos continued.
November
With more machines and more work to fill them, the team needed to grow too. In November we were pleased to welcome two new team members to our Production department, and we are still recruiting! There are currently vacancies for an experienced CNC Miller/Programmer/Setter/Operator, an Estimator & Account Manager, and a Production Leader to join our team.
December
As the decorations go up and mince pies appear in the canteen, the end of year reflections begin. 2021 has been a tough year for everyone, and yet… the Penta team has pulled together, and delivered for our customers, and for each other. We set ambitious targets, and we’re on track to hit them. We are planning for next year, with even more ambitious targets. And our targets are not just around the numbers. At Penta, we live and breathe our 3Cs: we communicate well, we take care, and we are consistent, and with a focus on continual improvement we know there is always more we can do.
So, if you got this far, thanks for sticking with me! It’s been quite a year, and even if I’m the only one to read this blog, it has been cathartic to take a look back and take stock. 2022 surely promises more challenges, and we look forward to meeting them head on.
See you on the other side!